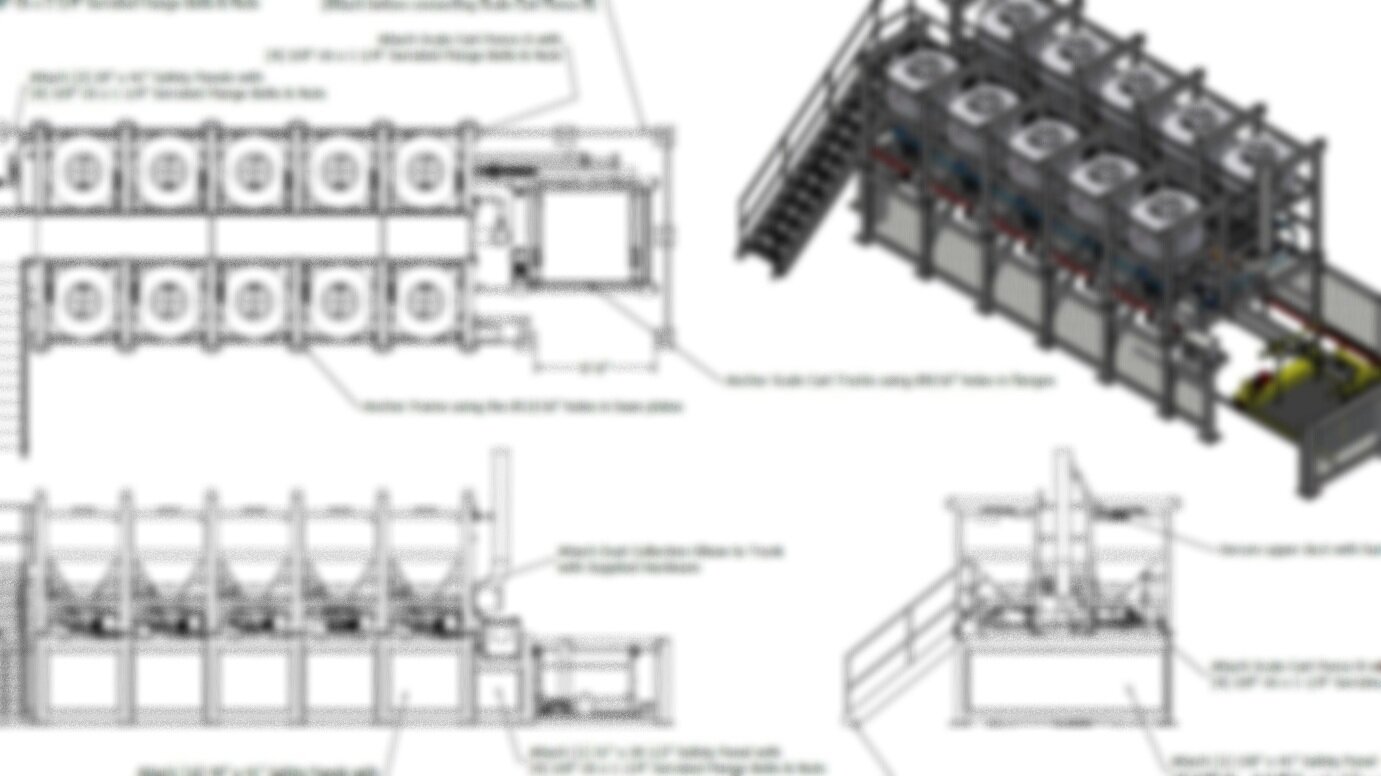
Case Study:
Zedmark
Bulk bag system increases refractory manufacturer’s batching accuracy
When manually handling paper bags required heavy lifting in a dusty environment, a refractory manufacturer switched to a bulk bag batching system.
Zedmark’s Slippery Rock, Pa., refractory plant receives truckloads of bulk bags containing materials such as aluminum oxide and zirconium oxide. The oxides come in different grades that vary according to particle size and material form (such as tabular or calcined). Forklift trucks move the palletized bulk bags to a warehouse and then to processing. During processing, raw materials are formulated into batches and mixed in a horizontal plow mixer. The mixed batches are placed in portable bins and moved to casting production lines. Finally, the batches are cast into specialized refractory shapes that are eventually used to manufacture glass, steel, cement, and aluminum products.
Manually handling paper bags results in dust, bag disposal costs
Before 1992, Zedmark’s batching station consisted of two workers who weighed and dumped a lot of paper bags into a mixer for each batch.
Zedmark received 50- and 100-pound bags of materials on pallets, which forklift trucks moved to a raised platform in the blending area. Workers lifted the bags and loaded them into a bag-breaking station mounted on load cells. The workers weighed each ingredient as it entered the station and discharged each ingredient individually into the mixer.
Zedmark’s concerns about the batching station included dust in the workplace, the time and manual labor required to formulate batches, the cost of material lost from spillage and incomplete bag emptying, empty bag disposal costs, and batch consistency. “Workers manually handled the bags, and we had some dust in the workplace as a result,” said Zedmark engineer Bob McCutcheon. Bags sometimes tore, increasing dust and material loss. “Bag disposal also got very expensive,” McCutcheon said.
Manufacturer seeks new batching system
In 1992, Zedmark wanted to develop a system to replace the manual batching station. Because Zedmark uses 16 basic raw materials in about 30 formulas with up to 7 raw materials each, the company sought a batching system that would accommodate their variety of production needs. “We were looking for a flexible system that would rapidly switch between formulas,” McCutcheon said. “We also wanted to eliminate manual bag lifting and dust,” he added.
Zedmark also had limited floor space and found that some batching systems required a separate weighing station for each ingredient, which would take up too much room. Then Zedmark considered a more compact system that used bins mounted on load cells. The system also permitted quick changeover between batching formulas and computerized batching, which Zedmark preferred. As a result, Zedmark approached the batching system’s manufacturer to discuss design options.
Computerized batching system uses PLC, PC
After initial meetings with the batching system manufacturer, McCutcheon started work on a custom-designed system. The resulting system has eight online bulk bag stations and a paper-bag or drum-dump station for very minor ingredients. All nine stations mount on load cells for loss-in-weight measurements that enable an IBM PC with an Allen Bradley PLC to control the materials as they discharge onto a transfer belt conveyor to the mixer.
Each station consists of a bulk bag holding rack that suspends the bag by four loops on a frame above a bulk bag dispenser, which is also supported on its own frame. Each frame is independently movable by forklift truck for quick material changes. Each rack includes a dust collection ring that goes around the bag throat to control dust during initial bag opening. Each station has a dust collection valve, and a worker opens the valve to open a bulk bag. Once the bag is opened, the air space between the bag and the station is sealed and the valve is closed . The bulk bag dispenser discharges through a flexible sleeve and a slide gate.
Because of Zedmark’s variety of batch formulas, the batching system includes eight additional bulk bag dispensers to increase system versatility. The system uses a bin ID system to prevent the interchangeable dispensers from being placed in the wrong station. Now the computer can tell which material is in which discharge station and weigh out the required amount of the right material. “That’s one of the features everyone likes,” McCutcheon said. “It reduces the potential for making a mistake.”
The bin ID system identifies each bin with a binary code in the form of a mechanical bar code; the code consists of a notched plate that trips limit switches to identify the bin. “The code identifies that such-and-such bin has such-and-such material in it,” McCutcheon said. The bin IDs are changed every 9 months on average.
To formulate a batch, the operator selects the formula and the number of batches to be repeated. A 3-digit pneumonic identifies each formula, and the operator can enter and store new formulas and pneumonics on disk. The operator inputs the desired batch size, and the computer receives information from the load cells to determine if enough of the required materials are present to formulate the batch. If so, the computer controls dispensing of each material in the required ratio to the transfer belt conveyor. The computer also controls the transfer conveyor and the mixer to finish the batching cycle.
Batching system cuts labor and cleanup costs
Since installing the batching system, labor needs have gone from two workers 10 hours per day to one worker 4 hours per day, and the plant is cleaner. The batching system also eliminates material loss due to incomplete bag emptying and empty bags.
Batching consistency has doubled, and Zedmark’s quality control department says batches are now always in specification. All programming and training for the system were supplied by the batching system manufacturer and done on site. A support person was also provided to help with the startup. The system has been operating for almost 2 years, and it has proven so efficient that Zed mark will move it to its Dover, Ohio, operation and do all batching for both facilities there.
“We’ve been getting visitors just to see the batching system, and the folks in Slippery Rock are upset that we’re going to move it to Dover,” McCutcheon said. “They were beginning to feel like they were in charge of a sci-fi vehicle or something.”
As seen in Powder and Bulk Engineering, October 1994.