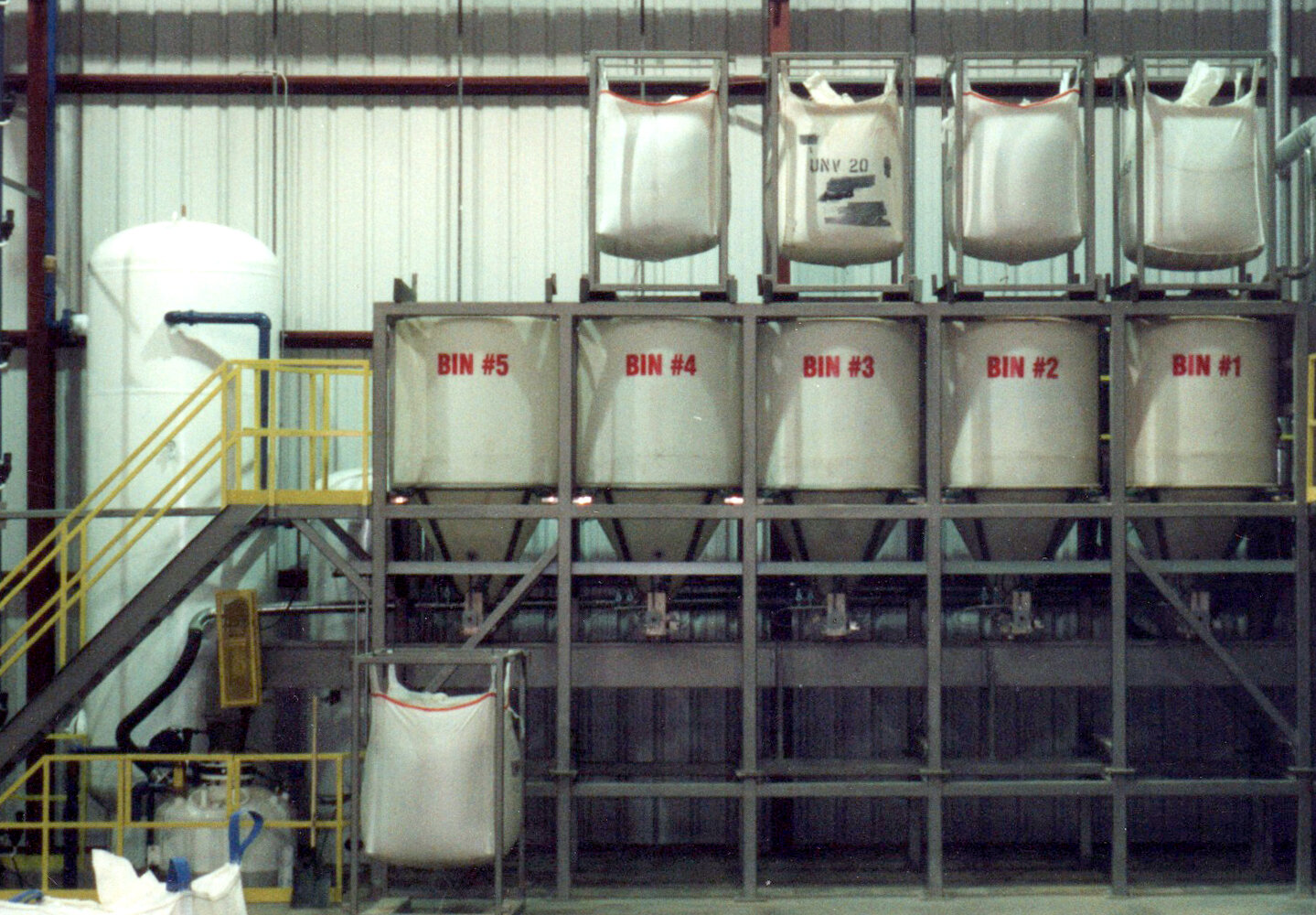
Case Study:
Universal Specialties
Automated Mineral Batching System Increases Productivity and Improves Worker Safety
Universal Specialties (Coraopolis, PA) a division of Universal Refractories, develops and manufactures specialty refractories for the steel and other industries. The company originally used a manual batching process, with the raw materials in paper bags. Problems occurred with inconsistent bag weights, bag disposal and high labor costs due to work-related injuries. Universal Specialties wanted to solve these problems, and increase production to meet customer demand.
WANTED: Quality Control
The original batching process required workers to empty hundred-pound bags onto a conveyor that delivered various powder raw materials to a mixer. Workers charged a belt conveyor with the required raw materials by means of paper bags. This conveyor then loaded a mixer, which mixed the raw materials. After the mixing cycle concluded, the mixer gradually discharged the powder batch contents into a paper sack bagger. Finally, the bagger operator filled paper sacks with product until the mixer was empty. This procedure usually lasted more than 30 minutes, and operators had to wait until the process was complete before starting a new batch.
This process posed several problems. In addition to the length of production time required, there was a high potential for worker injury. Additionally, an experienced worker was needed to make daily changes to the charging bin. This added time and labor costs to the production process.
Another problem was that the quantities of powder raw materials going into a mix varied with each batch due to inconsistent bag weights and laborers not ensuring that each bag was completely empty.
“Since the superior product demanded by our Quality Control Department was difficult to achieve, a change to the production process was needed,” says Shawn Elliott, Director of Research and Quality Manager.
An Automated Solution
Universal Specialties began looking for other viable options that would improve quality and consistency and decrease manual labor. After reviewing numerous options, Universal Specialties contacted Ingredient Masters, which specializes in powder batching systems.
“Ingredient Masters visited our facility, listened to our needs and exceptions, and offered a readily available, cost-effective alternative to our powder batching process. Their plan included integrating our existing equipment with new equipment. This plan did not require extensive modifications to our system or work environment, explains Elliott.
Ingredient upgraded the way primary powder raw materials were received, replacing hundred-pound paper sacks with bulk bags of 2,000 to 3,000 pound capacities. After a mixer completes a cycle, it discharges its entire contents into the bulk bag – an operation that requires two minutes, compared to the previous 30 minutes. The bulk bags of powder material are stored in 70 cu. ft. dispensers that produce many batches before refill is required. This reduces the labor needed for each batch.
Each dispenser is scaled with the aid of load cells and a pneumatic valve linked to a PLC/computer interface. This interface stores formulations, records batching and mixing times, and handles raw materials additions. It can also generate a spreadsheet detailing individual amounts of raw materials used in a particular mix, and total usage for a given production run. This data helps ensure that powder raw materials are consistent between batches.
Other raw materials that are a small portion of the batch size are staged at a bag break station. This station, also equipped with load cells and pneumatic valve, allows the operator to load the material into a storage hopper. The computer helps ensure accuracy for this manual operation. When all powder materials are in place, the computer verifies the weight and the operator can start the batch.
This automated system provides Universal Specialties with reduced manual labor and injuries, consistent product, and extensive control data. Additionally, using bulk bags instead of paper bags provides Universal Specialties a more cost-effective way to supply product to customers. “We consider this solution vital to the growth of our company,” concludes Elliott. “The advantages of such an automated system begin at a much more basic level than computer control.”
“The savings start by lowering the risk of injuries on the job (particularly back injuries). There is much less waste generated from spent paper bags, and raw material costs are reduced by bulk bag packaging. Production has increased 70% to 80%, while labor costs have decreased approximately 30%. The cost of one back injury easily pays for this system, and the additional benefits will only accumulate.”