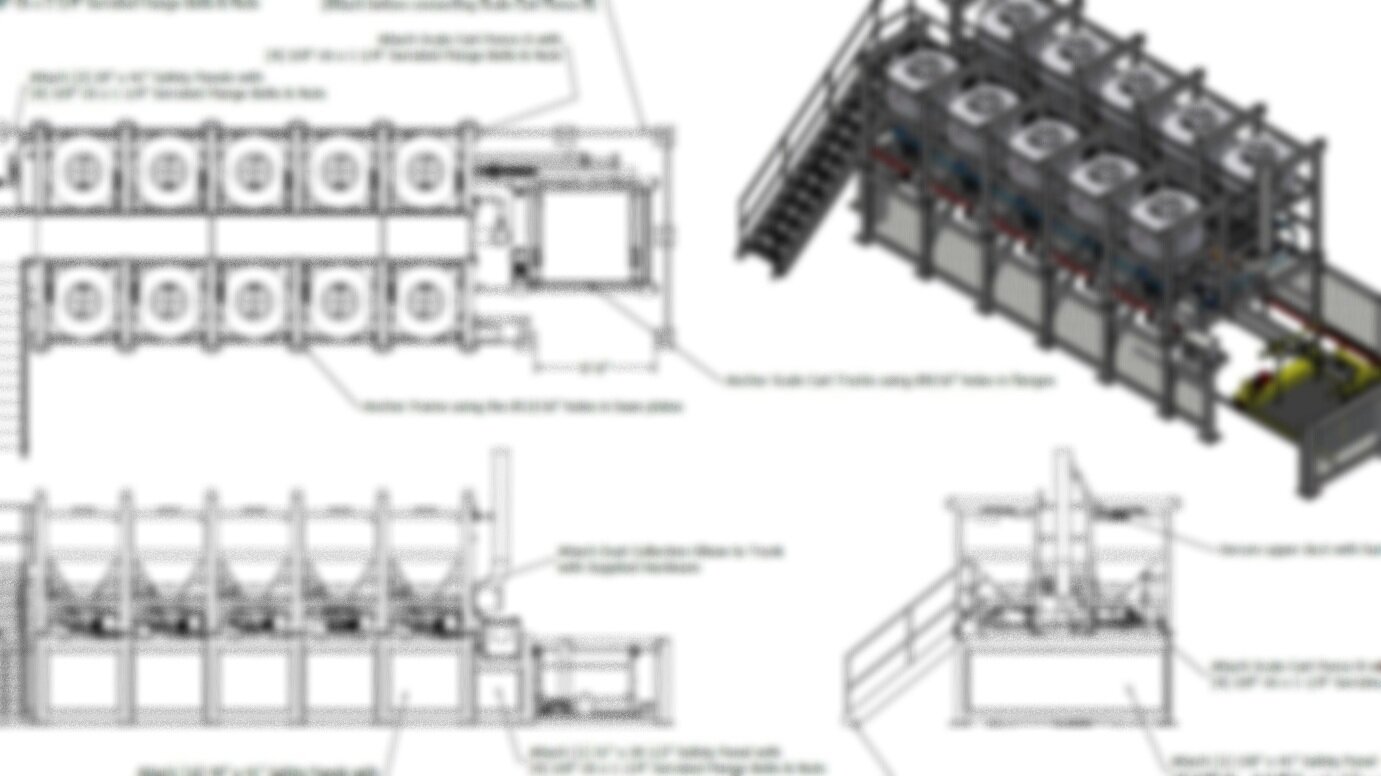
Case Study:
Spar Inc.
Automated material handling system provides efficient, trouble-free ingredient batching.
A refractories company installs an automated batching system to improve its production process.
SPAR Inc., Jacksonville, Ala., produces various dry refractories consisting primarily of natural ceramics for high-temperature applications, such as lining or insulating furnaces, kilns, and incinerators. Some refractories contain very hard ingredients that can withstand temperatures exceeding 3,000°F, while other refractories contain lightweight ingredients that have good insulating properties. Depending on its formula, a refractory can have various amounts of up to 18 different ingredients, ranging in weight from 30 to more than 3,000 pounds and in size from small particles up to large aggregates. The company was batching the refractory ingredients manually, but was experiencing problems such as production line bottlenecks and ingredient waste. It needed to find a way to automate the process to increase production capacity, improve product quality, and reduce waste.
Making a refractory
“After an operator secures a batch bag on the robotic cart, the cart travels under the hoppers and through the unloaders’ frames on a stationary track, stopping at predetermined discharge stations to receive ingredients.”
The company keeps the various refractory ingredients in 3,500-pound-capacity bulk bags, which are stored in a warehouse until needed. A formula specifies each ingredient’s weight and the order it’s to be added to a batch bin. After all the required ingredients have been added to the bin, a forklift moves the bin to a mixer, where the ingredients are discharged into the mixing vessel, then mixed together to make the final product. The refractory discharges from the mixer and is transferred to the packaging area, where the company can package it in various weights, ranging from 50-pound paper bags up to 3,500-pound bulk bags, depending on the customer’s requirements.
In the past, an operator used a forklift to individually move each ingredient’s bulk bag from the warehouse to the batch bin, which was located on a gain-in-weight floor scale. After positioning the bulk bag above the bin, the operator opened the bulk bag’s discharge valve to allow the appropriate ingredient amount to discharge into the batch bin. When the scale registered the correct ingredient weight, the operator shut the valve and checked off the ingredient on a printed copy of the refractory formula. The operator then returned the bulk bag to the warehouse. This process was repeated for each ingredient required to make the refractory.
Batching operation problems
Jim McClellan, SPAR vice president, says that as the company grew and added new products to meet the needs of its expanding customer base, it began experiencing problems with its production line. “The batching operation was causing production bottlenecks because it could take upward of thirty minutes just to add seven ingredients to the batch bin,” he says. “The forklift had to drive back and forth multiple times from the warehouse to the bin, and then the operator had to manually open the bulk bag’s valve and monitor the ingredient amount filling into the bin, which also caused some problems.”
If the operator put too much of an ingredient in the batch bin, the excess would have to be shoveled out to ensure the proper weighment. Or if too little was put in the bin, the operator would have to manually add more. “However, there were times when the operator didn’t notice that the wrong ingredient amount was added to the batch bin, and we typically didn’t detect it until after the mixing was finished,” says McClellan. “When this occurred, we were sometimes able to make a correction if we knew what ingredient was overfilled or underfilled. But more than likely we ended up throwing away the entire batch because it wasn’t the product the customer ordered.”
Looking to automate
In January 2007, McClellan talked with Donnie McClellan, the company’s president and owner, about the situation, and Donnie told him about a supplier of automated material handling systems. “After Donnie first started the company, he had looked at some of the supplier’s equipment and still had a few brochures and equipment drawings from that time,” says McClellan. “So we reviewed the brochures and went to the supplier’s Web site for additional information. We had looked at air-transport systems with scales and even considered hiring a mechanical contractor to design and build a system to our specifications. But when we saw a video on the supplier’s Web site showing how their automated batching system operates, it was evident to us that they had exactly what we needed.”
McClellan talked with other people in the refractories industry and heard many positive comments about the supplier’s systems. He contacted the supplier, Ingredient Masters, Cincinnati, to see if a system could be designed for the SPAR plant. “I told the supplier’s sales engineer about our batching operation and the ingredients we use, and that we needed a custom- de s igned sys t em wi th customized software,” says McClellan. “We didn’t have to send any ingredients for testing since they do a lot of work in the refractories industry and are very familiar with our ingredients’ characteristics. We did, however, send them plant drawings detailing the plant’s available floor space, ceiling height, and existing systems to help them better design the system. They were very responsive and flexible in handling our requests for customization — their answer to our requests was always ‘Yes’.”
The company approved the system drawings the supplier provided, and McClellan ordered one automated batching system. In June, the supplier sent the new system to the company’s plant, and the company’s engineering crew installed it in less than 1 week. “The system arrived in two major sections, so it was easy to position everything where we wanted it and bolt it together,” says McClellan. “After we finished the installation, the supplier’s control specialist traveled down here to set up and fine-tune the system’s PLC and computer and to show our operators how to use the system. By the end of the week, we were up and running at full-scale production levels.”
The automated batching system
The automated batching system consists of 9 double-row bulk bag unloading stations, 18 specially designed bag-lifting frames, 18 polyethylene dispensing hoppers, and a robotic cart with a gain-in-weight scale. A PC control station, which uses an Allen Bradley programmable logic controller (PLC) with RSView and RSLinx software programs and a Microsoft Access database, controls the system’s operation and enables communication between the equipment and the control station’s computer.
Each unloading station’s frame is about 12 feet 6 inches tall, 5 feet wide, and 5 feet long. An unloading station holds two 70-cubic-foot-capacity dispensing hoppers and two 5-foot-6- inch-tall bag-lifting frames, each of which mounts directly above a dispensing hopper. When the lifting frames are in place, an unloading station is about 18 feet tall. The unloading stations are installed in a straight line, forming two rows with nine dispensing hoppers each.
After an operator secures a bulk bag in a lifting frame, the frame is picked up by a forklift at its base, lifted about 12 feet, and placed onto an unloading station directly above a dispensing hopper. The operator then manually opens the bag’s discharge spout to gravity-discharge the ingredient into the hopper. Each hopper contains airjet, air-pad, and vibratory assemblies to facilitate ingredient flow from the hopper. A computer-controlled pneumatic slide-gate valve on each hopper controls the ingredient flowrate, using three different flow positions — one bulk and two dribble.
Each ingredient discharges in a specific quantity from a hopper through a short length of tube into a batch bag that sits on the robotic cart. The hoppers are unique in that each has a concentric bottom cone instead of a true cone-shaped bottom, so an ingredient discharges to one side of the hopper bottom rather than from its center. This allows the two hoppers in an unloading station to be nested together, nose to nose, so that their discharge tubes are separated by only 24 inches.
The robotic cart travels under the hoppers on a stationary track, stopping at predetermined points (discharge stations) to receive an ingredient. As an ingredient flows into the batch bag, the robotic cart’s gain-in-weight scale weighs it in real time and sends the information to the control station. The control station controls the ingredient flowrate from a hopper, activating the hopper’s pneumatic valve to change the flowrate at a predetermined weight.
McClellan says that when an ingredient first starts discharging from a hopper, the hopper’s valve is open 100 percent for bulk feeding. As the ingredient weight in the batch bag gets close to the set weight, the valve closes to the first dribble-feed position to slow the ingredient flowrate. When the ingredient weight is almost at the set weight, the valve closes to the second dribble-feed position, slowing the flowrate even more to accurately discharge the remaining ingredient. The valve closes completely when the set weight is achieved.
“The batching system’s control station, located next to the unloaders, controls and monitors all stages of the batching operation, sending the data to a computer that maintains real-time ingredient inventory records.”
A dust pick-up in each hopper captures fugitive dust created when a bulk bag discharges, and two dust pick-ups at each discharge station capture fugitive dust created when a hopper discharges an ingredient into the batch bag. The dust pick-ups in the hoppers operate continuously, but the discharge station dust pick-ups don’t. They operate only when the robotic cart is in position at the discharge station and from the time the cart departs until it arrives at the next station. After a batch’s dry ingredients have all been discharged into the batch bag, the cart stays at the final station for about 30 seconds to make sure that all of the fugitive dust has been removed from the batch bag. The fugitive dust is pulled into the company’s dust collection system.
Using the new batching system
When a bulk bag is empty, the system alerts the operator so that a full bulk bag can be moved from the warehouse and lifted into place. After opening the bulk bag’s discharge spout, the operator walks to the control station and enters the bulk bag weight into the RSView screen, and the PLC adds it to the weight of the ingredient remaining in the hopper. Next, the operator accesses a Microsoft Access pull-down menu and selects a refractory formula, which creates a job order that’s assigned a unique number for quality-control tracking. The database records all ingredient discharge amounts for a batch under this number, as well as the time the batch is completed.
The operator then puts an empty batch bag on the robotic cart and activates the system, sending the robotic cart down through the discharge stations to receive the required ingredient amounts. The system has electric sensors and other safeguards so that if an operator gets in the cart’s path, the system will automatically shut down.
Before the cart receives an ingredient at the first discharge station, the control station tares the cart’s gain-inweight scale, then opens the hopper’s valve and the appropriate ingredient amount discharges into the batch bag. If any discharge amount falls outside a preset ±3-pound accuracy range, the PLC stops the batching process and alerts the operator. The control station’s computer maintains inventory records and keeps a running tab on the ingredients used. This allows the computer to tell the operator at the control station when a bag is empty or when there isn’t enough of an ingredient in a hopper to complete a batch. The computer records everything at all stages of the batching operation, so if a problem should arise with an ingredient in a finished product the company can trace that ingredient back to the original ingredient supplier.
After the batch bag is filled, it returns to the starting point near the control station where the operator verifies the bag’s weight before the forklift moves it to the mixer. On average, a batch bag weighs about 2,800 pounds before it goes to the mixer, but can weigh up to 3,500 pounds for larger orders. “For most of our refractories, we’ll use the system to put anywhere from four to seven ingredients in the batch bag,” says McClellan. “If we need to, the system allows us to accurately weigh out as many as eighteen different ingredients. And most of the drops, which are in excess of one hundred fifty pounds, hit right on the money within plus or minus eight ounces. When less than fifty pounds of an ingredient is required, we’ll weigh it out on a different scale and then manually add it to the batch bag.”
Improving refractory production
Since installing the automated batching system, the time required for the company to make a batch has decreased by a little more than half. “With the new batching system, we can fill a batch bag in about eight to ten minutes, which has eliminated the bottlenecks we experienced with the manual batching process,” says Mc- Clellan. “Now we’re able to continue expanding our refractories product line and meeting our customers’ demands without having to work overtime. The system has also increased the accuracy of the ingredient amounts going into the batch bag, which has improved the quality of our final products. Being able to weigh each ingredient more accurately has also eliminated waste, allowing us to reduce our production costs and waste factors.”
The system’s ability to store each batch’s data “helps us maintain our inventory and purchase ingredients before we run short,” says McClellan. “In the past, there were times when we ran short of an ingredient because inventory wasn’t kept as accurately. This was due to human errors that occurred by calculating inventory at the point of finished goods instead of at the point of consumption in the manufacturing process. Our inventory records are much more accurate now.”
It’s easy for the company to change out an ingredient in an unloading station if it has to add a different ingredient into a refractory. “After we remove the existing bulk bag, the robotic cart rolls down to the unloading station and the hopper discharges any remaining ingredient into it,” says McClellan. “Then we lift the new bulk bag and lifting frame onto the unloading station and move the previous bulk bag to our ingredient storage area to use later. We still use the forklift to move bulk bags around the plant, but its use is mainly confined to the batching system, so there’s a lot less forklift traffic through the plant, which has reduced our fuel costs.”
“The supplier has been wonderful to work with — their service has been tremendous and they’ve bent over backward to help us,” says McClellan. “They’re one of the best companies I’ve worked with, and we’re completely satisfied with their batching system. It’s reliable and has been maintenance- and trouble-free, and it was easy for the operators to learn how to use it.”
As seen in Powder and Bulk Engineering, April 2008.