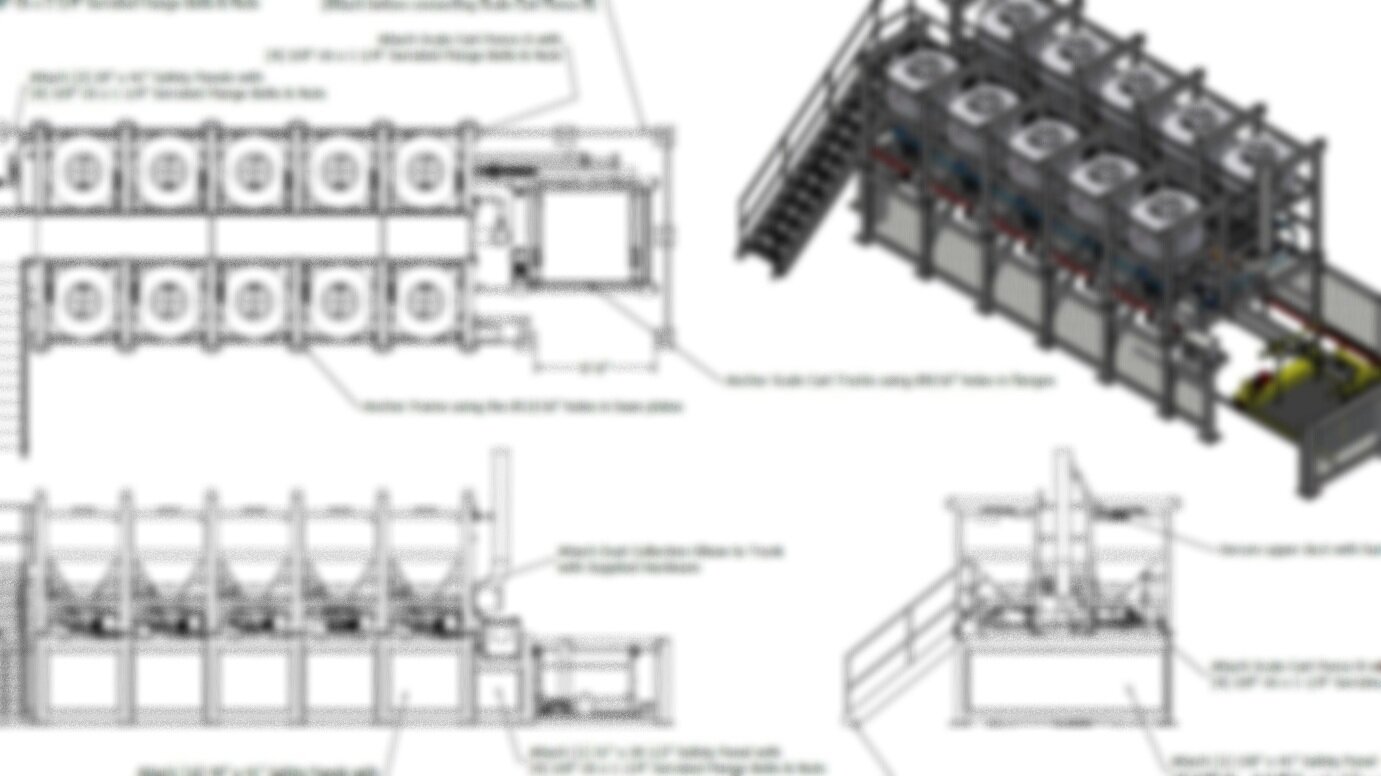
Case Study:
Oceanside Glasstile
Better Handling
A new material handling system is helping one glass manufacturer reduce costs and processing time while improving product quality.
Oceanside Glasstile® is a world leader in the design and production of handcrafted glass tile. Headquartered in Carlsbad, Calif., the company transforms raw sand and recycled bottles into luxurious, functional glass tile and mosaics for walls, floors, countertops and pools. Products are sold through more than 1000 retail showrooms throughout the U.S., UK, Western Europe and Japan. The stunning worldwide growth of the upscale housing market, along with the product line’s ready adaptability to custom design, has helped Oceanside Glasstile grow at double-digit rates for several years.
In late 2004, with production holding near historic highs and new products ready to emerge, the company decided to improve a major facet of its operations-the way powdered ingredients were received and handled. Oceanside Glasstile hoped to reduce mixing time, total process cycles and labor costs. It also sought to improve the tracking of ingredient use, and therefore color consistency between batches.
The first design concept that the company considered was a fully automated batch charging system engineered by a San Diego firm. However, the system’s $800,000 to $1 million price tag meant that the return on investment would be far in the future-far enough that the technology it was based on could easily become outdated before that benchmark was realized.
A fundamentally different concept was engineered and proposed by Cincinnati-based Ingredient Masters. It was a manual system, yet it offered many of the speed and efficiency advantages of a fully automated format. And the cost was less than $200,000, turnkey. According to Oceanside Glasstile Purchasing Manager Mike Taylor, “We thought they must have missed something, but that was the actual price.” It was time to see what the engineers in Cincinnati had in mind.
Outdated Handling Process
At the time of these discussions, Oceanside Glasstile received 10 major dry ingredients and 14 minor chemicals in 50-lb paper bags. Incoming material was manually emptied into one of four 55-gal drums, each accommodating 300 lbs of material. Drums were rolled and mixed in a process that required 30 minutes per barrel (7 hours total) before the material could be transferred to a bagger. It was then inverted, put on a pallet and staged at the furnace, where each 4200-lb batch would await processing.
The manual handling of bags and drums meant continuous lifting for employees, as well as significant dust generation from the dragging and dumping of the bags. Manual beam scales were used to weigh ingredients, but the system had no provision for printing or archiving batch information. Material use was tracked manually by the operators.
Improved Operations
Oceanside Glasstile evaluated an Ingredient Masters system in operation at a manufacturer of solid surface acrylic countertop material. Fully computerized, the 20-unit batching system featured a digital scale cart that moved between 20 dispensers according to one of 200 programmed recipes. Flow rate and ingredient weight values were consistently accurate to within .5% or better. The system was local network-compatible and radio frequency identification (RFID)-capable.
After a favorable evaluation, Oceanside Glasstile gave a formal nod to the Ingredient Masters proposal. At the system’s core are 12 70-cu-ft (1400-lb) hopper dispensers, referred to as “day bins,” which hold a day’s worth of material. Rotationally molded of polyethylene, the bins allow easy viewing of material levels. Polyethylene dispensers also remain “sweat-free” when temperatures fluctuate, a major benefit since ingredients can be hygroscopic. The dispensers have a liquid-smooth interior, which, combined with the dispenser’s geometry, facilitates good flow for most ingredients. Ultra-fine colorant powders are notoriously flow-resistant, so vibratory pads, which use pulsed air to fluidize the material, were also provided.
A 2000-lb-capacity “super sack” is suspended above each dispenser. These flexible woven polypropylene sacks are UV-treated, reusable and economical, and they’re provided in a variety of fabric weights to meet specific tensile strength requirements. Super sacks can also be handled with forklifts, eliminating ergonomic stressors and the tearing and disposal of paper bags, and they are a substantial space saver in the plant. A separate rack holds 8- and 3.5-cu-ft dispensers containing sufficient quantities of minor ingredients to last up to 30 days.
When the operator is ready to run a batch, he uses Microsoft Access to print a “pick sheet” that shows the required major and minor ingredients. The ability to do this on the shop floor, rather than involving office personnel, is a substantial time saver.
A hopper-bottom bin is loaded on a digital scale cart, which displays the formula and needed elements. The cart is driven to the first dispenser required for that batch and loaded. A signal is sent to the system PC, recording in Excel format the material dispensed. The scale is then reset and driven to the next dispenser. The real-time record keeping is useful for inventory management and batch tracking. When all ingredients are dispensed, a report is generated and the bin is locked under a mixer. It is rotated for 10 minutes, then positioned on top of a screw auger. The bin bottom releases and the auger feeds the material into the furnace.
The time from design approval to the commissioning of the Ingredient Masters system was 16 weeks. Process recipe programming and controls interface were completed five days later. “If you can get what you need with a simple solution, you’re clearly ahead,” Taylor says. “The fully automated system sounded good, but it lacked some flexibility and was costly. We liked this design, which has very few moving parts. There’s very little to break, and stocking replacement parts is simple.”
Additional Benefits
Dust, always a challenge for dry material processors, is collected at every station when material is dumped, as well as at the bottom of the hopper-bottom bin when it is lowered for furnace charging. Dust collection, and subsequent reuse of collected particulate, is an integral part of the Ingredient Masters design. It also reduces “housekeeping” chores and contributes to improved indoor air quality and a good work environment.
Oceanside Glasstile has been a “green” company by design since it was founded in 1992. It is now able to reclaim the vast majority of its glass melt trim and edge material, something that was never possible with the old system. Material is crushed and stored in a day bin. The PC is programmed to allow a given percentage of re-melt per batch, and it calculates the revised quantity of virgin ingredients based on the rework material available. Recycled bottle glass is also a primary ingredient. Some products are made of up to 85% recycled glass.
In terms of efficiency, “Our time to make a batch went from 75 minutes to 10 minutes,” says Taylor. “We now feed 4200 lbs into a furnace in 2 minutes instead of several hours, since we use three hoppers rather than 14 drums. The efficiency gains here have been huge. There’s far less material handling, no more floor sweeping, and the hazardous waste burden of silica is far less. Workers no longer have to struggle with drums and 50-lb bags, and no one has to stand in front of a 2200°F furnace, chucking in 4200 lbs of material. Our material accuracy is .5% or better, and, as a result, our colors are more consistent.”
Planning for the Future
The company has also made plans for various contingencies. A bag break platform was installed so that if a future ingredient is only available in 50-lb bags, it can be quickly loaded into a super sack, put in a lifting frame and be ready for use.
“And if we ever want to fully automate, the Ingredient Masters design makes that an easy step,” says Taylor. “We already know the cost-about $100,000-which is still less than a third of what the original company wanted to charge.”
As seen in Ceramic Industry, November 2006.