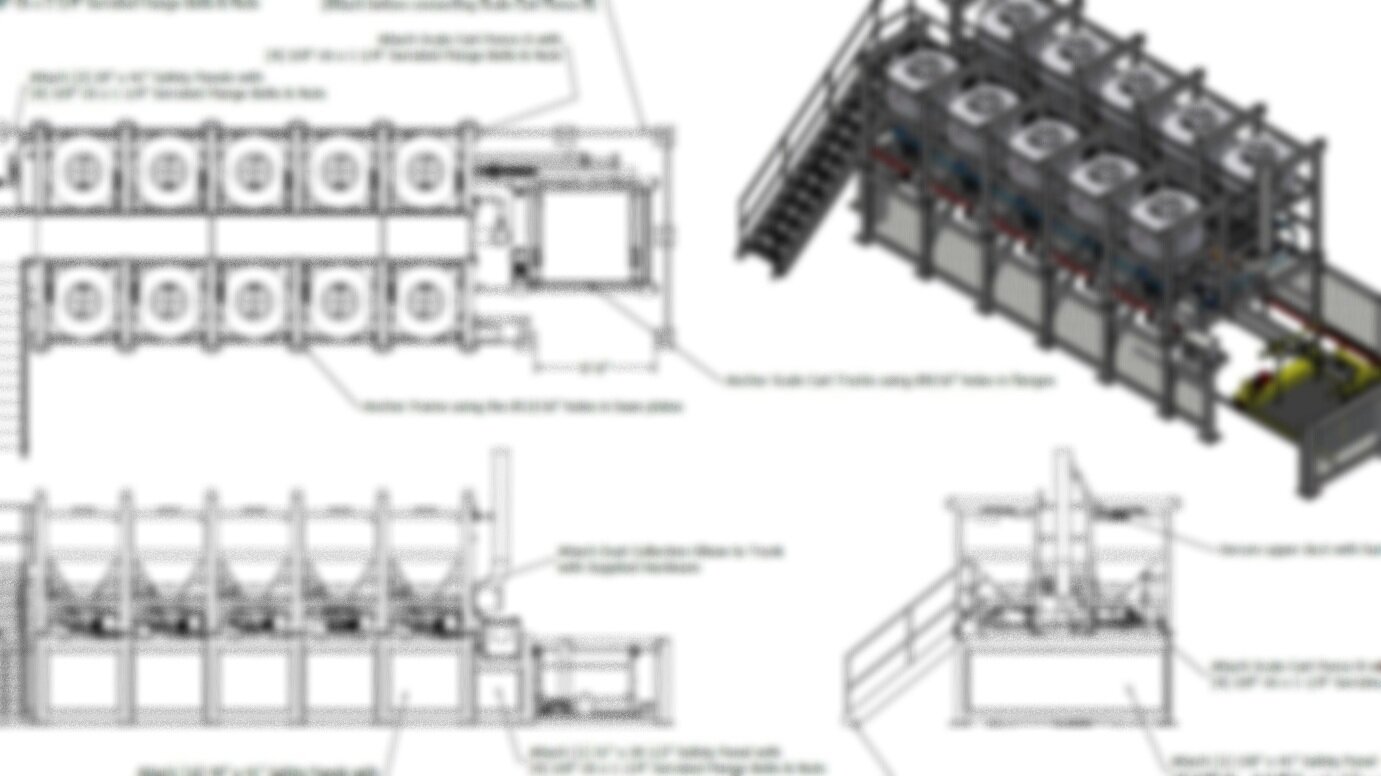
Case Study:
Morganite Crucible Inc.
Improving Production with Automated Batching
A new, fully automated batching system has improved accuracy, efficiency and dust collection for one well-known refractories manufacturer.
Batching large quantities of fine materials can be difficult, especially for companies that handle their batching operations manually. Common problems with manual batching include production inefficiencies, dust control and inaccuracies in the amount of ingredients added to a batch. As a result, many companies are beginning to view automated batching systems as a valuable investment with a relatively quick payback.
Such was the case for Morganite Crucible Inc. in North Haven, Conn., a manufacturer of high quality crucibles used in the aluminum, copper and copper alloy, steel, and precious metals industries for metal melting and holding. Three years ago, the company operated a manual batching operation that stretched onto three floors and required 2 ½ people to operate. According to Dave Okamoto, operations manager, batching inaccuracies and dust control were two of the plant’s biggest challenges. An automated batching system has helped solve these problems while also increasing production efficiency and reducing labor requirements.
Manual Batching Problems
Manual batching was a complicated, error-prone process for the refractories manufacturer. “We had to take super sacks of material up an elevator to the third floor and dump them into the hoppers using an overhead monorail crane,” Okamoto said. “On the second floor underneath the hoppers, an operator rode on a manual batch car that featured an integrated scale. The operator would watch the scale, and when enough material had entered the hopper, he literally had to put a bar in the valve, yank it and try to close it on time to get the right amount of material in each batch. This process was subject to a great deal of inaccuracies since it was very dependent on the reflexes of the operator.”
Dust was also an issue. “A typical hopper is roughly the shape of an upside-down pyramid. In that design, the material sometimes compacts as it’s going down and creates a bridge, which will hold it’s own weight in the hopper while the material underneath falls out,” Okamoto said. “We literally had to beat large sticks against the hoppers to loosen that material, but when the bridge of material finally collapsed, it created a big dust cloud. It almost looked like a heavy fog with some of the days and other materials we were dealing with.”
Frustrated by these problems, the company began searching for an alternative. In 1998, the company president John Maxwell, visited another refractories plant that had installed an automated batching system from Ingredient Masters Inc., headquartered in Cincinnati, Ohio. According to Okamoto, Maxwell was impressed with the way the system operated.
“Their operations were very similar to ours, and we were eager to see if we could achieve the same benefits,” Okamoto said.
An Automated Batching Solution
In 1999, Morganite Crucible installed a new, custom-designed, 28-unit, freestanding automated batching system from Ingredient Masters. An improvement in batch quality was noticeable immediately.
“We’ve been able to significantly increase our accuracy with the new system,” said the Okamoto. While other changes within the plant-such as a new, high-intensity Eirich mixer-have also led to quality improvements, Okamoto has no doubt that the automated batching system has greatly reduced inaccurate batches. “We used to lose around eight hours per week just in bad mixes, but we no longer have that problem because our mix is consistent,” he said.
The design of the new system also eliminated the material bridging problem and associated dust emissions. “The system is really sophisticated, starting with the geometry of the hopper. Instead of having a pyramid shape, these hoppers have three sloping sides paired with one shear wall-kind of like a pyramid in which one side has been shoved over,” explained Okamoto. “This design keeps material from bunching up inside the unit. An air bladder that’s mounted on the side of each hopper pulsates and introduces air into the material to keep it moving. And an air screen located near the bottom of the hopper blows across the slide gate, loosening the material and keeping it from accumulating around the slide gate.
“The machine also has its own separate dust collection system,” Okamoto added.
While the company currently uses just half of the 28 units in the new system, Okamoto is confident that the extra capacity will come in handy in the future. “We set the system up thinking that we were going to double it in size somewhere down the road, and we knew it would be a lot more cost-efficient if we made the deal for the 28-unit system to start with,” he said.
Additional Benefits
In addition to increasing the plant’s hatching accuracy and reducing dust emission, the automated batching system has also increased production flexibility, reduced manual handling of the raw materials, and reduced labor requirements.
“With our manual batching system, each batch was taken directly from the weighing hopper to the mixer, where an oil ingredient was added,” explained Okamoto. “Once the dry and liquid components were mixed together, the batch had to be used almost immediately to prevent it from aging. The new system, on the other hand, batches directly into a super sack, enabling us to keep an inventory of batched dry materials. We typically keep about three days’ worth of inventory on hand. If we want to dean our batch system or do an upgrade, or if something goes wrong with the system, the inventoried batches enable us to maintain our production levels without unnecessary downtime.”
The system also features a manual addition station for additional production flexibility. “Our batches are typically composed of 24 ingredients, and most of these are automatically picked up by a cart and added to the batch. But there are still some cases where we want to be able to add materials manually. The manual addition station allows us to mix and match certain batches, or add a new ingredient without going through the trouble of in a new hopper and reprogramming everything,” said Okamoto.
The freestanding design of the system makes for easier material handling. “We no longer have to take big, heavy bags up in an elevator and muscle them around. Instead, we simply mount a super sack to a frame, and then use a forklift to lift it on top of this free-standing structure,” said Okamoto. This process greatly reduces the chance for operator injury compared to the manual batching operation. And because the system is completely automated, fewer employees are needed to run production operations. The company now uses a 1 ½ man crew, instead of the 2 ½ required with the manual system.
The company has gained additional storage space as well. Because the new system is freestanding, the company has been able to convert the third floor of its facility into a storage area.
Overall, Okamoto views the new system as a definite benefit to Morganite Crucible’s manufacturing operations. “The new system has provided us with increased product accuracy and production flexibility, reduced dust emissions and labor requirements, and a number of other benefits. It has definitely been a good investment for our company,” he said.