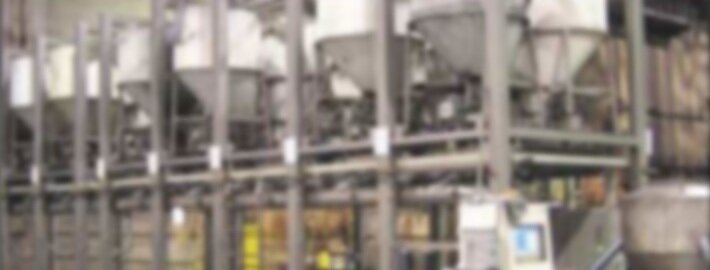
Case Study:
Morganite AM&T
Polypropylene Sacks Reduce Costs
Benefits include improved batch accuracy, shorter batch times
Morganite AM&T of Coudersport, PA manufactures mechanical bearings and seals for jet engines (including Pratt & Whitney) and critical fluid handling applications, including pumps for fuel, chemicals, and drinking water.
Morganite manufactures in specialty volumes: typical raw material batches are 600 lbs. Recipes are custom-engineered by Morganite and generally include four or five powdered components (cokes, graphites, specialty chemicals) plus binders. Each ingredient has an accuracy-by-weight tolerance of eight ounces or less.
Until recently, some raw materials were loaded from 55 gallon drums, one at a time manually, using a lift truck. The process took 15 minutes on average. In addition to being time-consuming and labor-intensive, the process that was complicated by individual materials’ flowability and other characteristics. Changeover routines, dust emissions and vessel cleaning were other issues.
In 2000, Morganite Development Engineer David Brown brought his production team to Chicago’s annual Powder & Bulk Solids trade show to investigate alternatives. As options were evaluated, the closing of a Morganite subsidiary in North Haven, CT, proved fortuitous for Brown’s team.
The Connecticut facility manufactured crucibles from powdered materials for the aluminum, copper alloy, and precious metals industries. Material batching was accomplished using a batching system engineered and manufactured by Ingredient Masters, Inc., Cincinnati
The North Haven system had 24 raw material dispensers each 54 cu. ft., manufactured from virgin polyethylene. The Ingredient Masters dispenser design is unique. Rather than the traditional pyramid shape, these dispensers are round, with sides sloping to a shear wall drop. This design feature minimizes dust emissions and prevents the bridging effect that occurs wherever powdered ingredients are used.
“Super Sacks” Replace Drums and Paper Bags
A key component of virtually all systems designed by Ingredient Masters is the replacement of drums and paper bags with “super sacks” for incoming raw materials – and for inventorying batched materials when needed. These polypropylene sacks, which hold up to 3000 lbs of material, reduce unit material costs, require less storage and simplify issues with dunnage and landfilling. Super sacks containing raw material are mounted to a frame and fork-lifted to the dispenser. A rail-mounted scale cart moves between dispensers according to the process recipe; material is discharged into the cart through Salinas Vortex stainless steel pneumatic slide gates with special adapters for fine powder metering.
With 24 dispensing stations, system capacity was 25 percent larger than the Coudersport facility required at the time. But in yet another fortuitous development, Ingredient Masters agreed to buy back the excess stations (in the end, six were re-purchased, after Morganite opted to keep some additional units to accommodate growth.)
The batching system was disassembled and moved to Pennsylvania in February, 2003. Modifications implemented at the time of re-assembly included raising the system two feet so that existing batching boxes could be used and installing an uninterruptible power supply to assure operation in event of power anomaly.
Collection hoods integral to each dispenser collect fugitive dusts to common ductwork connected to an existing pulse jet. Material, which is primarily carbon, is collected at a central point and ultimately sold to a steel mill, making this otherwise-wasted by-product a profit center in itself.
Load cells installed on the batching carts monitor ingredient weights discharged at each station. In event of under of over-feed an authorized operator must over-ride and approve the program to continue.
New Ladder Logic Established
To update the controls, Brown worked with Ingredient Masters’ controls engineer, Peter Hohorst. Hohorst installed Rockwell’s RS View with graphic interface onto a PC-driven PLC, and established new ladder logic. Marrying the PLC’s instant communications with the PC’s archiving capacity gave the system exceptional accuracy and speed, along with virtually unlimited recipe storage
The system is straightforward to learn and use. Operation is password-protected at multiple levels of authority. A specially designed, fully washable keyboard provides the best-possible accommodation to the plant environment.
Each hopper has its own icon indicating the weight of powder it contains; alarm lights indicate when replenishment is needed. At the start of a cycle, the system checks hopper inventories to assure there’s enough of each raw material and will not permit a start if any amounts are insufficient.
Station number boxes on the screen change from gray to red if the recipe requires he ingredient and the PLC has calculated a discharge amount for the station. The station box changes to white with a red border if the station is inactive as a duplicate.
Ingredient codes are listed on the right side of the screen. The color of the names changes from white to yellow if the recipe calls for that ingredient.
When a station valve is open, the color of the valve icon changes from gray to red. The net batch weight is indicated as a bar graph on the cart body. Operators can adjust valve opening positions and activate various types of vibratory devices and air pads to facilitate better flow if needed. The number of repeats is calculated using data from the match that was run most recently. A batch is started by clicking the Start Batch button under the appropriate recipe. An ingredient check for a job order is initiated by clicking the Check Recipe button.
When a batch cycle is complete, the PLC produces a permanent batch record that includes all ingredients and their respective weights, and assigns a lot number. In the future, a feature will be added that monitors raw material usage. Capability will also be added to automatically download batch record data into a separate database. Forms that allow operators to queue batches in a sequence, a week at a time, will also be added.
Re-installation and commissioning of the Ingredient Masters system was completed in a few weeks. The new system produced significant recurring benefits in improved batch accuracy, shorter batching times (the average cycle is just five minutes-1/3 of what was required by the previous, manual system), the reduction of manual labor, and better housekeeping due to more effective control of fugitive dusts. Better overall ergonomics and the elimination of workplace injuries- particularly back stains from the loading of ingredients- is especially noteworthy.
There is also a broader view. “We had a major re-organization this year,” Brown explains, “and understand very well how having manual labor involved in what is very competitive manufacturing process can make a company vulnerable to outsourcing. By using labor resources most efficiently, this plant has become less vulnerable, while producing a product that is of highest quality and consistency.”