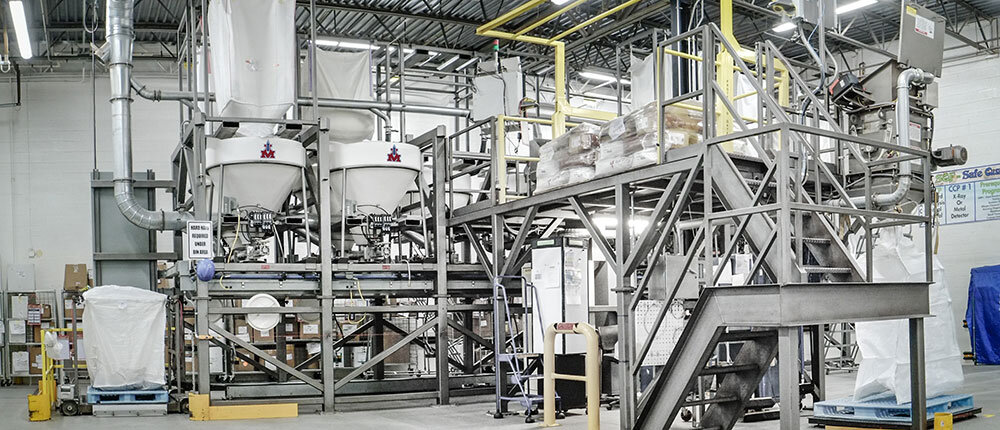
Case Study:
Medifast, Inc.
New bulk batching system offers Medifast significant increases in efficiency with added accountability benefits.
Medifast is a meal replacement system for dieters who want to control their weight but still be able to enjoy their meals. The system offers pre-packaged replacement meals that are nutritionally sound and calorically-controlled so that the company’s clients, when following the plan, lose weight consistently.
From a production standpoint, the company’s strength in being able to offer an extensive and varied menu of meals with numerous options presents a substantial challenge for preparing those meals in an efficient manner. Additionally, providing consistently delicious meals for the company’s clientele also means maintaining absolute control over the ingredients so that quality is assured.
Part of the company’s meal processing and fabrication is handled by a batching line in which ingredients are combined and then blended before exiting the facility. The company had been using a batching system in which most of the work was done manually, with many of the ingredients being added from 50-lb sacks. The efficiency of the process was complicated by the fact that the menu of meal choices consists of over 100 recipes, which combined used a staggering 250 different ingredients. A typical recipe uses anywhere from fifteen to forty different ingredients and creating a 2,000 lb. batch typically took 4.5 hours when done manually. Additionally, the company recognized that along with the inefficiency of the manual batching procedure, tracking of ingredients was subject to a greater chance of human error.
The decision to go with automated weighing and batching
Because Medifast was experiencing steady growth in the sales of its products, company production managers began to take a look at their manual batching system with an eye to upgrading. The decision was a calculated one but deciding how exactly that would be done required extensive planning. The company’s engineers looked at three or four modular systems but found nothing suitable for their needs. Then, through one of their packaging suppliers, they heard about Ingredient Masters, who had extensive experience in just the type of custom solution Medifast was looking to implement. One advantage the Ingredient Masters system offered was the use of off-the-shelf components so replacement or upgrades would be simplified.
As far as evaluating suppliers, Colin Jesien, (Plant Manager) of Medifast, said, “We looked at a lot of out-of-the-box systems and didn’t really have much luck. Ingredient Masters convinced us they were the right choice with their ability to provide an entire system. It had out-of-the-box components but everything can be upgraded. The ability of their system to grow with us was one of the strong reasons why we decided they would get the project. And the customer service was excellent. They were open to suggesting best practices they had seen but they always said, ‘This is up to you. It’s your decision.’ They really provided a lot of valuable input.”
When it came time to install the equipment, Medifast faced some space constraints in their facility. Says Mr. Jesien, “We had a low ceiling in a section of our manufacturing facility and the engineers at Ingredients Masters were able to work around that with some smart decisions on where to place individual dispensing bins to give us maximum efficiency.”
A system with elegant simplicity
The Automated Batching System that Ingredient Masters designed, fabricated and installed for Medifast is a gain-in-weight bulk batching system. The system utilizes a platform scale cart traveling on food grade polyurethane wheels through the dispensing zone to seven (7) dispensing stations. A frame is built onto the scale cart to hold a bulk bag that is used as a batch bag that receives a discharged recipe batch. On the superstructure above are positioned twelve (12) 30 cu. ft. dispensers, all with automatic orifice valves. Due to the powdery nature of many of the ingredients, the dispensers have air pad fluidization equipment built in to ensure free-flowing ingredients.
Bag lifting frames are used to discharge bulk bags of raw materials into the 30 cu. ft. dispensers. The lifting frames are hoisted by fork truck and fit securely into channels in the superstructure. One dispenser position is located in an area with a low ceiling that prevented use of a bag lifting frame for refilling. The dispenser placed in that spot can be lowered to ground level with a fork truck for refilling.
Some raw materials need a little extra attention due to clumping and are conditioned before they are added to a dispenser. Incoming paper bags filled with raw material are loaded on a mezzanine platform and emptied into an Eirich conditioner. A new, empty bulk bag (mounted in a lifting frame) is filled through the fill head on the bottom of the conditioner. This bulk bag of conditioned material is now raised into place over a dispenser to be discharged into the dispenser.
In addition to the major dispensers, the system has two bag break stations for the addition of minor ingredients, such as kosher and non-kosher food and spice items. The scale cart has proximity sensors so that it positions accurately under the individual dispensers. Two Human Machine Interface touch-screen displays, one at ground level and one on the mezzanine for the bag break stations, are used for controlling and monitoring the system. A bar code on each bulk bag allows data to be collected on all batched recipes for lot tracing. The system is capable of dispensing ingredients down to a tolerance limit of +/- 0.5 lbs per ingredient draw.
The system also has a dust control system that keeps the facility cleaner and helps prevent stray ingredients from contaminating batch recipes.
When the recipe is ready to be batched, the computer-controlled scale cart, equipped with a bulk bag, travels to the far end of the system and stops under the appropriate dispenser. The system then automatically dispenses the appropriate ingredient in the precise amount needed and the cart travels to the next position.
When the bulk bag has been loaded, the batch is transferred to the mixing area to be blended thoroughly. The bulk bag batch is transferred to a lifting frame so that it can be loaded into an Eirich Optimat Blend FPB-125 Fluidizing Paddle Blender. The blended batch is discharged into a bulk bag and moved to one of seven packaging lines.
Efficiency and quality control were the driving motivations
The Ingredient Masters system allowed Medifast to purchase many of their raw materials in bulk bags as opposed to the 50-lb bags used with the manual system. This change improved the material handling ergonomics for the employees by reducing the number of 50-lb bags handled. The company had hoped for some cost savings by buying material in bulk, but the primary cost savings benefits came from improved labor efficiency through less bag handling, higher yields of the ingredients and reduced raw material packaging disposal costs.
Mr. Jesien says about the batching system upgrade, “We use the new system for proportioning out all of our bulk ingredients. We’re using it for efficiencies but also for the quality aspect of it. We can track all the ingredients from the time they arrive to our facility through final packaging, giving us an important lot tracking capability for quality control. We also like the inventory reporting we get from the system.”
As far as efficiency, Mr. Jesien said, “On loading the blender, we’ve seen about a 30 to 45% increase and another 50 or so percent increase in proportioning efficiency. We saw the biggest increases in our set-up function.”
Positioned for a bright future
Medifast was able to increase the efficiency and raise the quality of their batching operation by implementing the Ingredient Masters Automated Bulk Batching system. Mr. Jesien addressed the decision and its impact on the corporation’s operations. “We wanted to be on a three-year ROI and I think we’re under that. But, make no mistake, this was set up primarily as a quality function from the beginning.”
Medifast, the diet replacement meal company, had a lot to gain by looking at a new way of doing things and it is paying off.