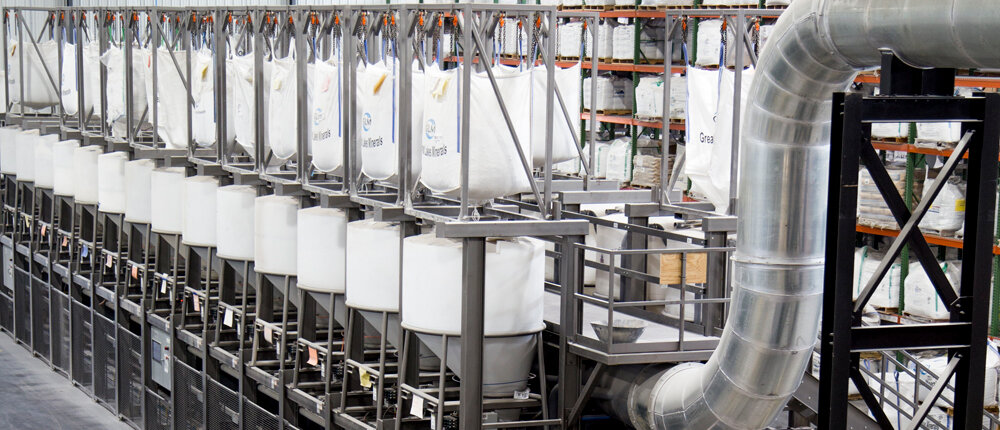
Case Study:
HarbisonWalker International
Largest US Supplier of Refractory Products and Services Looks To Ingredient Masters For Batching System In New, State-of-the-Art Monolithic Refractories Manufacturing Plant.
Harbison Walker International (HWI) announced in February 2017 that it was building a new, technologically advanced $30 million refractories plant as a key step in its strategy to continuously improve performance and better respond to the future needs of customers and the marketplace. As the largest supplier of refractory products and services in the U.S., HWI’s undertaking was no small endeavor.
Fast forward to spring 2018 and HWI was already shipping products, having opened just one year after breaking ground and within its planned schedule and budget. This remarkable effort – to create the most advanced refractory facility in North America and, likely, the world – has paid off by elevating product quality and consistency and having a positive impact on product availability, ordering, packaging, and support for HWI customers.
The Batching System Is Critical To Success
Behind the scenes, HWI’s team reinvented how they produced and delivered quality monolithic products, the fastest growing segment of the refractories marketplace. As part of that effort, the HWI team focused on a highly critical part of the manufacturing process— the bulk batching system. Ingredient Masters, a Cincinnati, Ohio based manufacturer of bulk material handling and powder processing equipment, has supplied automated bulk batching systems to U.S. manufacturers for handling a full variety of materials. Naturally, HWI was interested in how Ingredient Masters systems might contribute to process design and toward achieving program goals.
Automated bulk batching systems are designed to replace the very labor-intensive and imprecise process of hand-scooping or manually adding heavy bags of ingredients to a large recipe mix. Lack of precision when adding ingredients can lead to product quality and consistency issues among many other problems.
Collaboration Leads To Revolutionary Ideas
Ingredient Masters was granted an opportunity to pitch their automated bulk batching system as a keystone to the HWI plan. Compared to their competitors, HWI recognized that Ingredient Masters systems offered several advantages including a proven track record in refractory applications and a very willing engineering team ready to collaborate with HWI to deliver an advanced bulk batching system.
According to Kevin Ballard, Senior Director, Engineering and Maintenance Excellence at HWI, “Ingredient Masters has earned a solid reputation in bulk batching solutions and this gave us confidence that they would be able to deliver on the stringent specifications we needed. They also demonstrated a willingness to work with us in designing a revolutionary new plant and new processes for our industry that place a premium on quality along with employee health and safety.”
Douglas Hall, senior vice president, Integrated Supply Chain at HWI adds, “While some of the advanced technologies, processes, and equipment at South Point may be similar elsewhere, what makes this plant so outstanding is the ingenious design, engineering, and configuration of all these elements. This configuration, combined with our overall manufacturing approach is completely revolutionary.”
Ingredient Masters also worked with additional HWI equipment suppliers to integrate components from their existing equipment into the batching system to utilize the batching system’s controls and data acquisition.
System Provides High Throughput, High Accuracy and Maximum Uptime
The HWI system from Ingredient Masters features two identical batching line configurations consisting of rotationally-molded polyethylene dispensing hoppers. HWI has incorporated system redundancy and has the capacity to produce multiple batches per hour, consisting of as much as two tons of material. The Ingredient Masters system can store an unlimited number of recipes and can batch multiple recipes simultaneously.
Ingredient Masters designed an automated powered conveyor system to transport custom designed batch totes through the bulk batching system. The batch totes are equipped with RFID tags to continuously monitor their locations throughout the system. Using gain-in-weight load cells on the conveyors and computer-controlled discharge valves on the dispensers, the batch totes cycle through the batching system to receive the raw materials required for their recipe. The systems include minor ingredient add stations, where minor ingredient units dispense the smaller draws of raw material to allow the use of lower capacity load cells for higher accuracy.
Transfer Cars Handle Queueing To Blenders
Once the batch totes exit the batching system filled with their designated recipe, a system of four laser-guided transfer cars queue the batch totes in accumulation conveyor lines for one of three mixers. As emptied batch totes return from the mixers, the transfer cars also queue the batch totes in accumulation conveyor lines for re-entry to the bulk batching system.
Raw Material Refills Are Fast and Easy
Dispensing bins are re-filled using raw material packaged in bulk bags. Suspended in lifting frames, the bulk bags are positioned securely above each of the dispensers using a fork truck. The fork trucks feature an HMI interface – a slimmed down, custom version of the standard interface used in the rest of the system. The fork truck drivers are alerted to the status of each dispensing bin with color-coded material depletion alerts to help the drivers prioritize the raw material refilling process.
Mezzanine access allows an HWI team member to open the bulk bag bottom spout to release raw material into the batching system dispensers. Each dispenser features a dust mitigation pick-up to draw air from the top of the dispenser as it is being filled to control dust.
Full Traceability from End-To-End
The Ingredient Masters batching system offers complete traceability of raw material throughout the process. Any raw material introduced to the system is input via bar code and logged to its associated dispenser. As the raw materials are dispensed for recipes, the amount of dispensed material is logged into batch records. This tracking process provides end-to-end traceability.
Scott Culshaw, CEO, Ingredient Masters points out, “Traceability is so important to our customers. We give them that ability using a system featuring all “off-the-shelf” components – nothing proprietary – for easy maintenance and low cost. Our goal is always to create an easy-to-own system that will deliver on the needs of our customers.”
Controls…The Heartbeat Of The System
The system features a centrally located, state-of-the-art Allen-Bradley Rockwell Automation PLC with ethernet I/O modules strategically located near the field devices. Multiple touch-screen Operator Interface Panels are located throughout the system. Advanced predictive adaptive control algorithms are utilized to improve accuracy and throughput while decreasing process variability.
The batching system controls also communicate with the HWI ERP system for recipe, order sequence and batch data.
A Successful Partnership
“Our custom solution from Ingredient Masters is an integral part of our revolutionary manufacturing facility and optimizes our manufacturing efficiency, provides data for better analysis and decision making, and enables unparalleled product quality. Thanks to Ingredient Masters, we have been able to drive continuous improvement and achieve world-class accuracy in our batching system,” notes Ballard. He adds, “Their team has also been a valuable resource for our manufacturing team by helping us to capitalize on new opportunities.”
Mike Gasaway, President, Ingredient Masters says, “Working with HWI has challenged us to really think outside the box. We developed new processes and are proud that we met or improved on all initial projected timelines, production levels and accuracies HWI established. This system should give them the production speeds and efficiencies they need to help them retain their status as #1 supplier in the refractories industry for a long time.”