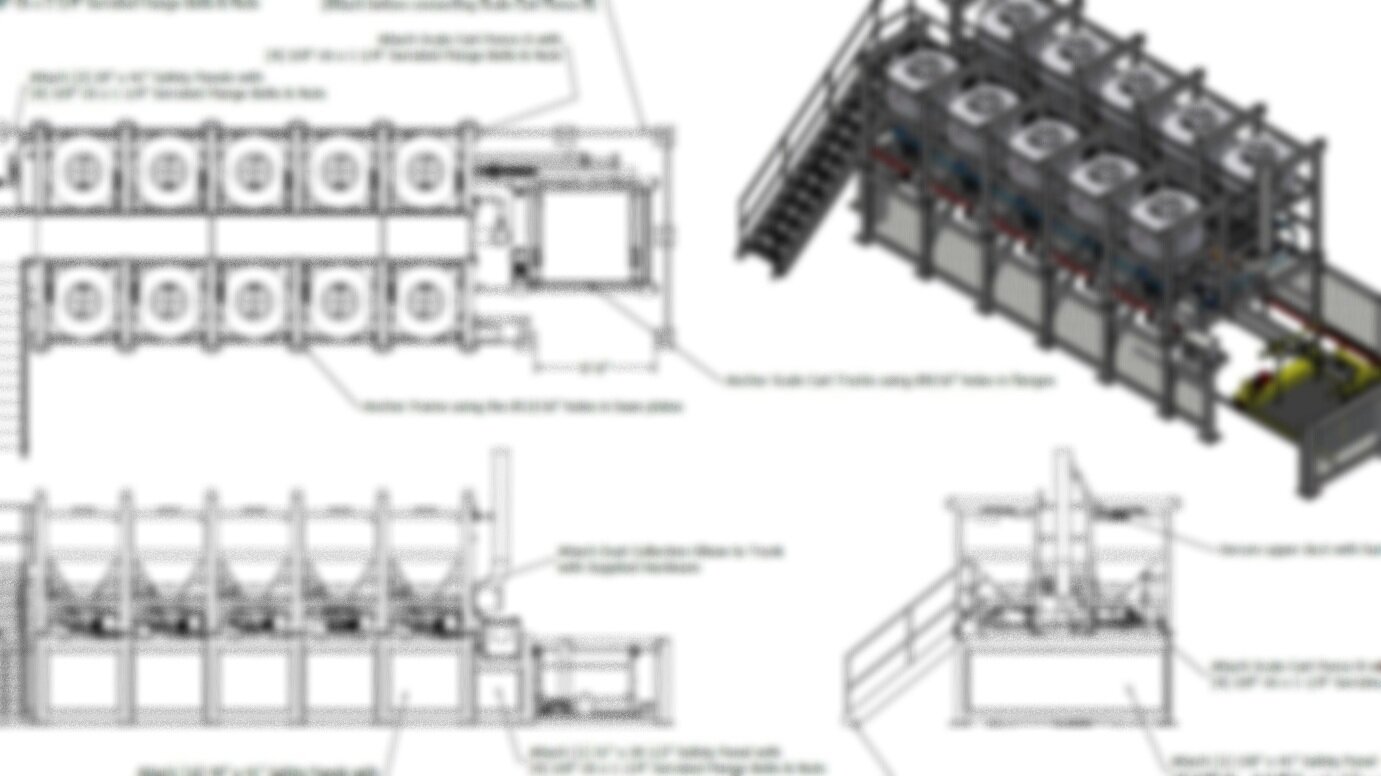
Case Study:
Eli Lilly
Automated System Makes Material Handling Easier
A pharmaceutical company installs an automatic material handling system to solve ergonomic, labor, and bag disposal problems.
Eli Lilly, headquartered in Indianapolis, produces pharmaceuticals. The company’s Animal Health Business Division operates a facility in Lafayette, Ind., and uses a fermentation process to produce Tylosin, an animal antibiotic. Handling the 50-pound paper bags that held the antibiotic’s dry raw materials caused ergonomic problems for the workers and excessive labor and bag disposal costs for the company.
The Lafayette facility operates 24 hours a day, 7 days a week, and receives more than 2 million pounds of various raw materials each year. Previously, a truck delivered the 50-pound paper bags of dry raw materials to the facility. The material suppliers palleted the bags according to material type and assigned lot numbers for identification and tracking purposes. When the ingredients arrived at the facility, a forklift removed the pallets from the back of the truck, and an operator verified and recorded each pallet’s lot number, material type, manufacturer, bag count, date received, and other information on a shipping ticket. The forklift then removed the pallets from the receiving area and stacked them in a warehouse for later use. Another operator verified the information, manually input it into the company’s main computer, and filed the shipping tickets.
Making the medicine
Each animal antibiotic lot consists of several batches of dry ingredients that are processed in a fermentation station. In the past, to prepare a batch an operator was given a manufacturing ticket that contained the batch’s specific material types and weights. In the warehouse, the operator used the ticket to select and then manually stack the required number of 50-pound bags for each material onto an empty pallet.
Unfortunately, a batch’s material weights were rarely specified in 50-pound increments. Mike Svenstrup, the company’s associate engineering consultant, says, “If one of the required materials in a batch was specified at one hundred sixty-seven pounds, the operator would put three fifty-pound bags on the pallet, then manually weigh the remaining seventeen pounds into a separate bag and place it on the pallet.”
After completing this time-consuming process, the operator verified and recorded each material’s weight before a forklift transported the pallet to a staging area near the appropriate fermentation station. The operator continued putting together batches of dry ingredients until the required number was staged. A second operator verified each batch’s material weights, entered the information into the company’s main computer, and filed the manufacturing tickets. The operator then opened the bags from the pallet and manually dumped the material into the fermentation station for processing.
Manual bag handling causes problems
Manually handling the 50-pound bags created three problems for the company. First, repeatedly lifting the bags could potentially cause injuries such as back and shoulder pain and carpal tunnel syndrome. Second, because of the time involved in gathering and measuring the ingredients, the company needed two operators working alternate shifts to prepare the batches. This kept labor costs high and material handling efficiency low. Third, bag disposal costs were high because of the vast number of bags being discarded. Eli Lilly wanted to find a way to minimize or eliminate the need to dispose of the empty bags. The company realized that automating its material handling process and switching to bulk bags could probably solve its problems.
Company searches for material handling system
In April 2000, the company did an Internet search for material handling systems suppliers, and, after reviewing all possibilities, narrowed its search to three suppliers. After a thorough investigation, which included presentations by the suppliers and visits to working installations, the company chose Ingredient Masters, located in Cincinnati. In the summer of 2001, the supplier’s technicians traveled to Eli Lilly’s facility to design the material handling system’s layout, taking into consideration the facility’s available floor space, ceiling height, structural obstructions, and existing systems. The supplier designed the entire system to fit between existing structural supports, maximizing the facility’s floor space. The supplier also integrated an existing dust collection system into the system. After Eli Lilly approved the supplier’s layout drawings and engineering prints, the supplier built the system at its plant, and in the fall of 2001, shipped the system to the facility. The supplier’s technicians assembled the system in the facility, tested it, and instructed the company’s operators how to use it.
The material handling system
The material handling system consists of 12 free-standing bulk bag unloaders, 12 bag-lifting frames, 12 receiving hoppers, and a robotic cart with a gain-in-weight scale. A PC control station, which uses an Allen Bradley programmable logic controller (PLC) with RSLogic 500 hardware and Allen Bradley RSView and RSLinx software programs, controls the system’s operation and enables communication between the equipment, the control station, and the company’s main computer.
Each bulk bag unloader’s frame is about 12 feet 6 inches tall, 5 feet wide, and 5 feet long. The unloaders each handle one dry ingredient and are installed back to back in a straight line, forming two rows of six. A 5-foot-6inch-tall bag-lifting frame that supports a 2,000-pound capacity bulk bag fits on each unloader’s top, making the assembled unit approximately 18 feet tall. Once loaded with a full bulk bag, the specially designed lifting frame is picked up by a forklift at its base, lifted about 13 feet, and placed onto an unloader’s top.
A 2,000-pound-capacity receiving hopper is mounted directly under each unloader’s top. The hopper is gravity-fed from the bulk bag hanging in the lifting frame. Each hopper has air-jet air-pad, and vibratory assemblies to break up material chunks and facilitate material flow from the hopper. A computer-controlled valve on each hopper controls the material flowrate. The material discharges in specific quantities from the hoppers, through a short length of tube, into a 2,000-pound-capacity lined batch bag that sits on the robotic cart.
The robotic cart travels under the hoppers and through the unloaders’ frames on a stationary track, stopping at predetermined points (discharge stations) to receive material. Two unloaders share one discharge station. As the material flows into the batch bag, the robotic cart’s gain-in-weight scale weighs it and sends the information to the control station.
A dust pick-up in each receiving hopper captures fugitive dust created when a bulk bag discharges, and two dust pick-ups at each discharge station capture fugitive dust created when a hopper discharges into the batch bag. The dust pick-ups in the hoppers operate continuously, but the discharge station dust pick-ups don’t. They operate only when the robotic cart is in position and from the time the cart departs until it arrives at the next station. After a batch’s dry ingredients have all been discharged into the batch bag, the cart stays at the final station for about 30 seconds to make sure that all of the fugitive dust has been removed from the batch bag. The fugitive dust goes into the company’s dust collection system.
Automating the material handling process
The facility now receives its various raw materials in 2,000-pound bulk bags. The raw material manufacturers still send a shipping ticket with the shipments for record-keeping purposes, but now a bar code on each bag specifies such information as the material’s lot number, material type, and manufacturer. After a forklift removes the palleted bags from a truck, an operator uses a bar-code scanner to scan each bag’s bar code. The scanned information is automatically sent to the company’s main computer for storage. The forklift then moves the bags to the warehouse and the operator files the shipping tickets because they contain additional information about various aspects of the manufacturing process.
When the process calls for an ingredient, the forklift removes a bag from the warehouse and an operator manually secures the bag in a bag-lifting frame. The forklift moves the frame to the appropriate unloader where the operator scans both the bag and the unloader’s bar code, sending the information to the computer. The computer checks the information and tells the operator if the correct bag is at the correct unloader. The forklift lifts the frame into place, and the operator manually opens the bag’s discharge spout to discharge the material into the hopper. When the hopper is filled, the material flow stops.
The operator then goes to the control station, accesses the main computer, and downloads a lot’s batch information. After verifying the batch information and entering the appropriate number of batches to be made, the operator puts an empty batch bag on the robotic cart and activates the system, sending the robotic cart down through the discharge stations to receive the required material amounts. The system has electric eyes and other safeguards so that if an operator gets in the cart’s path, the system will automatically shut down.
Before receiving material at the first discharge station, the control station tares the cart’s gain-in-weight scale, then opens the hopper’s valve and fills the batch bag. The control station records the weight received along with all of the material’s information. The control station transfers this information to the main computer, which maintains inventory records and keeps a running tab on the material used. This allows the main computer to tell the operator at the control station when a bag is empty or when there isn’t enough material in a hopper to complete a batch. The main computer records everything at all stages of the material handling operation, so if a problem should arise with a material in a finished product the company can trace that material back to the original material supplier.
After the batch bag is filled, it returns to the starting point near the control station where the operator verifies the bag’s weight. Preprogrammed parameters automatically tell the operator if the bag is within spec. If the bag is out of spec, the control station tells the operator what material is out of spec and by how much. The company’s quality control engineers will then make the decision whether or not to discard the batch. If the bag is in spec, the operator seals the bag’s liner and puts a cover over it. A forklift then picks up the bag and takes it to the fermentation process staging area. The system continues operating until the appropriate number of batches has been made.
System solves problems
The new material handling system converted a labor-intense manual process into a simple automated process. “The new system drastically reduced the need for the operators to manually handle materials,” says Svenstrup. “Now, the only manual processes the operators have to do are scan the bulk bag bar codes, operate the forklift, secure the bag in the lifting frame, open the bag’s discharge spout, and use the control station to download the batch information. In addition, we cut one operator from this process because it no longer takes so much time to piece together and dispense the material.”
Finally, Svenstrup says, “We eliminated the large number of paper bags that we previously had to dispose of, because the material now comes in lined bulk bags that are recyclable. We simply return the bulk bags to the manufacturer, so now all we throw out are the plastic liners, which is cheap and easy.”
Currently, Eli Lilly is only using 11 of the unloaders for its processing needs. But at any time, the process can be expanded to include the twelfth unloader, or the system can be redesigned and reprogrammed to accommodate several more.
According to Svenstrup, “Everything is working well. The material handling system is really simple to operate. There were some minor problems during start-up, but the supplier’s technicians traveled to our facility and worked hand-in-hand with us to fix them.”
As seen in Powder and Bulk Engineering.