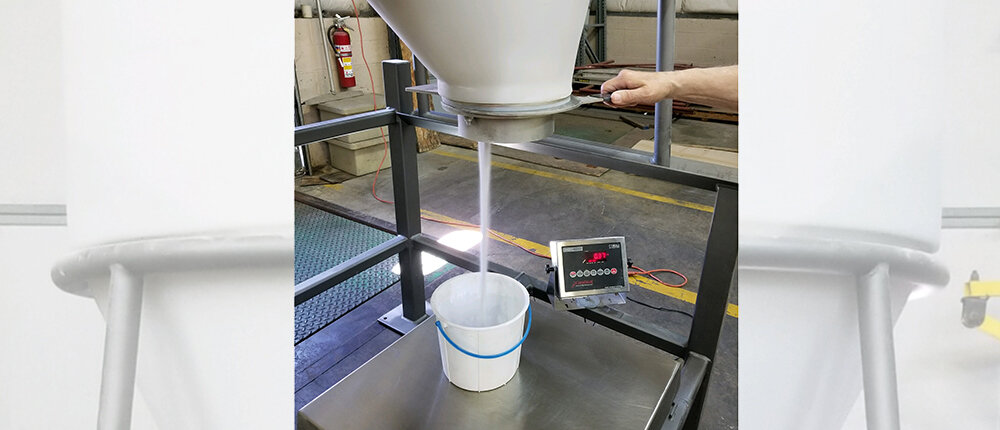
Case Study:
Comdess Company, Inc.
Single Ingredient Dispensing System Speeds Cycle Times and Improves Ergonomics For Plastics Molding Company By Eliminating Manual Scooping of Material from Gaylord Boxes
Comdess Company, Inc., a Seville, Ohio manufacturer of custom rotationally molded products, has been an innovator since its start in 1981. The company was home to the first fully-computerized rotational molding machine and continues to regularly test and evaluate equipment, materials, procedures and methods to improve their operations.
During one recent customer visit, an unexpected process improvement was discovered which led to new opportunities for both Comdess and their customer. While it is not unusual for customers to offer feedback to their vendors, this particular Comdess customer was very interested in the Comdess manufacturing process…specifically, the method used to measure and dispense pulverized polyethylene from bulk containers.
An expert in bulk batching systems, Scott Culshaw, of Ingredient Masters was checking out his company’s newest order of rotationally molded bins in production at Comdess when he noticed a Comdess employee manually scooping material out of a large, Gaylord container into a small buckets.
Culshaw spotted an opportunity for both companies. Ingredient Masters manufactures batching equipment that eliminates the back-breaking and hazardous job of manually scooping material from a bulk container. Comdess president, Sam Mandich, an enthusiast of efficiency, was very intrigued with what Culshaw had to say.
Hand Scooping: Slow, Physically Demanding, Low Accuracy
The rotational molding process is a high-temperature, low-pressure plastic-forming process that uses heat and biaxial rotation to produce hollow, one-piece parts. A measured quantity of pulverized polyethylene powder is introduced into the rotational molding machine. The machine heats a mold of the part to be produced while it rotates, melting the polyethylene. As the machine rotates through two or more axes, the melted polyethylene adheres to the mold wall.
The existing method for adding the pulverized polyethylene powder to the rotational molding machine was to scoop the material by hand from the Gaylord containers into small, 7.5 gallon fiber drums. This method was slow and physically demanding. As material was removed from the Gaylord container, reaching the bottom with a scoop required dexterity and balance. In addition, the accuracy of using a scoop was oftentimes a problem.
An Expert Was In The House
“Ingredient Masters engineers precision dry bulk batching systems for virtually any application from small, single ingredient dispensers to very large, fully-automated, multi-ingredient systems. And all of our systems use “off-the-shelf” components…that’s something our customers really love,” says Culshaw. “All Ingredient Masters systems are custom engineered for the project,” he adds.
A Simple Solution To Multiple Needs
The solution Ingredient Masters developed for Comdess was a single ingredient manual dispensing system. Consisting of a 70 cubic foot rotationally molded bin with a manual 304 stainless steel pivot point slide valve, the system allows an operator to meter material with ease and at a high level of accuracy. The pivot point slide valve was developed by Ingredient Masters and allows precise dispensing of material.
The dispensing system includes a custom two-part tubular steel dispensing frame. The upper part of the dispensing frame holds the bin and includes integral forklift slots to allow removal of the dispensing bin from the lower, base portion of the dispensing frame.
Comdess inventories 3-5 different color-compounded polyethylene mixes in individual dispensing bins. The two-part frame system allows Comdess to quickly and easily switch to a different mix when needed. Each dispensing bin includes a bin loading access port on top with a screw-on lid to prevent contamination and allow sealed storage of unused mixes.
The lower, base portion of the dispensing frame holds an electronic scale on which 7.5 gallon fiber drums receive dispensed material. Operators open the pivot point slide valve and dispense the desired amount of material quickly and effortlessly. The integral electronic scale helps the operator meter material accurately.
Easy Loading
Comdess receives their raw polyethylene material in bulk bags. Loading the dispensing bins with the raw material is simplified with a bulk bag lifting frame designed by Ingredient Masters. The bagged raw material is hung on the lifting frame and positioned over the dispensing bin using a forklift. An operator removes the lid to the top access port of the bin and inserts the bulk bag spout for fast loading of material.
To maximize efficiency of transferring raw material to the dispensing system, Comdess asked their pulverized polyethylene supplier to ship the raw material in 800 lb. bulk bags rather than Gaylord containers.
In order to keep raw material packaging costs down, Comdess requested that the bulk bags be re-used rather than tossed after one use. This change was the source of the biggest hurdle in switching to the Ingredient Masters system. The material supplier was reluctant to re-use the bulk bags for fear of raw material contamination, but after several successful trial runs, Comdess has been able to re-use their bulk bags up to 20 times.
The Results
* Comdess reports several benefits from switching to the Ingredient Masters dispensing system:
*Weighing accuracy has improved due to the ability to precisely meter material using the single pivot point slide valve system.
*Reduced physical requirements as a result of the change from scooping material from a Gaylord to simply operating the pivot point slide valve.
*Reduced prospect of contamination since the dispensing bin is sealed and is not constantly opened and closed to access material as was the case with the Gaylord containers.
*Spillage and material waste was reduced to virtually zero by eliminating the handling of material by scoop.
*Speed of cycle times improved considerably with the pivot point slide valve operation replacing multiple scoops of material from a Gaylord.
The system is also portable and Comdess can move it with a forklift to different parts of the plant when necessary.
After three years with the system, Sam Mandich, president of Comdess says “We used to actually physically get down into a Gaylord container to scoop out the last bit of material. The Ingredient Masters system has improved the accuracy and cycle time speeds for us and has helped us manage the increasing cost of our raw material. It’s allowed us to have a moderation of the price increases and has been a nice addition to our workflow.”