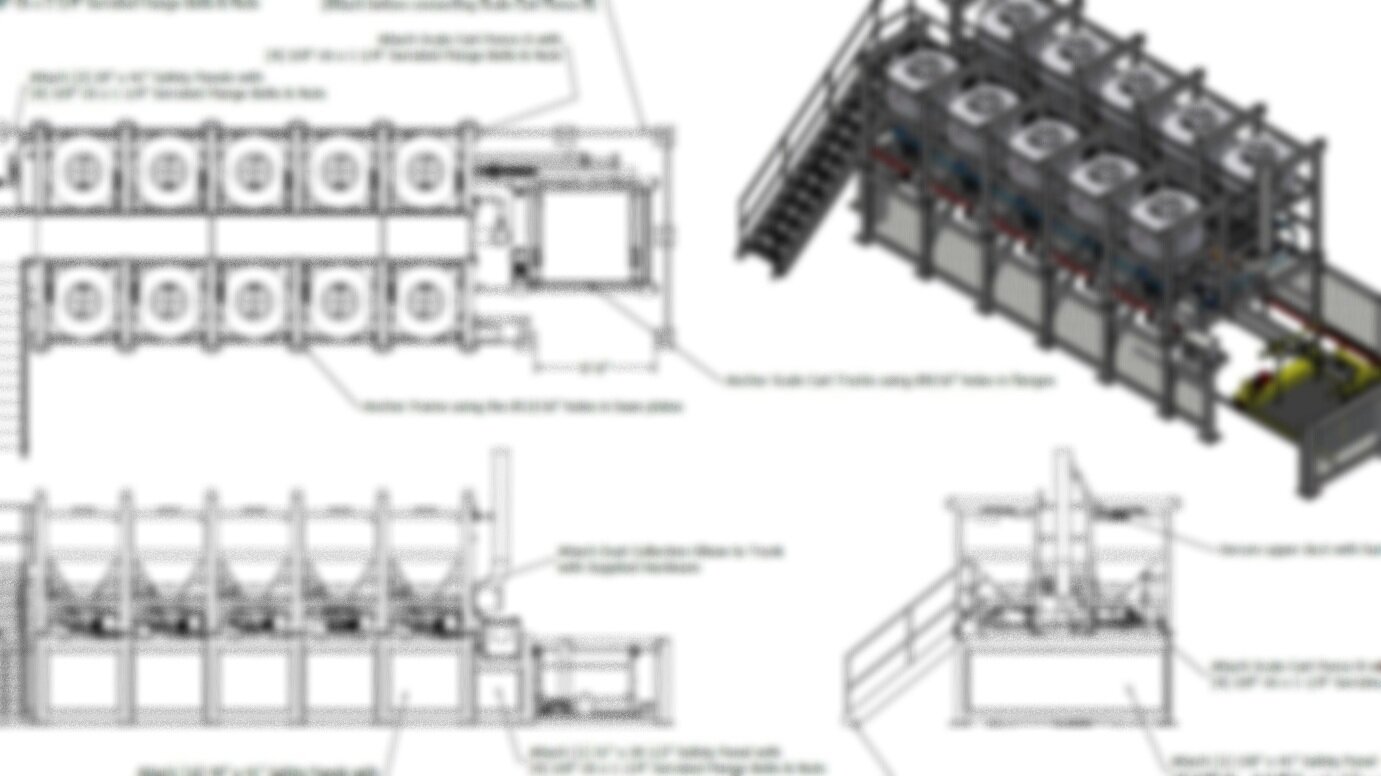
Case Study:
Cincinnati Tyrolit
Optimized Powder Batching
A new powder batching system has helped a manufacturer of abrasive grinding wheels improve its operational efficiency and competitive advantage.
Cincinnati Tyrolit manufactures vitrified (ceramic) bonded and resin-bonded grinding wheels for the grinding and polishing of tool and alloy steels. It is part of the Tyrolit Group, a diversified global entity that manufactures more than 50,000 products for cutting, grinding, drilling, honing, dressing and polishing.
Tyrolit, which supplies major bearing manufacturers, automakers and aerospace component suppliers, maintains several thousand product recipes. In late 2004, Tyrolit sought to improve the handling of the powdered ingredients used in the manufacture of vitrified bonds – its dominant product. The bond is a ceramic matrix of oxides, silicates, borates and phosphates that coats the abrasive grains (clays, frits and feldspar material), allowing them to fuse when pressed and fired at 2300ºF.
Vitrified bonds have gained popularity in recent years because of their aggressive and free-cutting structure and their ability to adapt to a broad range of spindle speeds with just minor adjustments. Vitrified bonds minimize wheel “loadup” and reduce the need for dressing and conditioning. This, in turn, has allowed the “G ratios” that are calculated for grinding wheels to move higher-a higher G ratio means a more efficient grinding operation. Both vitrified bond and resin bond systems have also benefited tool makers by letting them customize operations to customer demands and their own goals for output, which is a valuable flexibility.
Tyrolit’s goal was to eliminate the manual scooping of primary ingredients from 2000 lb. hoppers, and its attendant product waste, housekeeping and lessthan- ideal ergonomics. Other objectives included task simplification, greater efficiency and elimination of ingredient caking on the sides of the hoppers-a phenomenon that was costly in terms of both lost product and maintenance.
A Modular Solution
Bob Hegener, Tyrolit’s manager of Process Engineering, had twice encountered similar challenges; in both instances, he had worked with Ingredient Masters in Cincinnati, Ohio, a company specializing in custom powder batching technology, to design and implement a solution. He decided to turn this newest challenge over to Ingredient Masters as well.
The system engineered by Ingredient Masters includes 27 polyethylene dispensers (seven 54-cubic-foot units, eight 28-cubic-foot units and twelve 8-cubic-foot units). Polyethylene, which is abrasion-resistant and inert to most chemicals, is well suited to the application. It also provides an excellent moisture barrier, so caking would not be an issue.
An existing scale cart with electronic load cell sensors was enlisted to weigh each ingredient; a highly accurate manual valve replaced the task of scooping the required ingredients by hand.
Typical batches contain three or four ingredients. The cart moves beneath each hopper according to the product recipe, the bar code on each hopper is read, and the appropriate valves are activated.
When the specified weight is reached, the valve is closed. The system maintains accuracy at ±0.05 lb.
The Tyrolit system is designed to accommodate a 2000-lb bulk bag (“super sack”) above each 2000-lb dispenser. These bulk bags, which are manufactured by King Bag Co., Cincinnati, Ohio, use 7.4-oz. coated (“non-breathable”) material and have anti-sift seams to prevent the filter-through of fine particles.
Replenishing ingredients into the dispenser as they are used effectively eliminates the downtime required for changing out the hoppers. The replenishment feature also reduces product waste and contributes to a process area that is far cleaner than it was when it was used for filling metal totes. Custom, color-coded loops facilitate product identification and help ensure high product quality.
The batching system was engineered, manufactured and installed in six weeks, and was fully functional in 14 weeks, following the interface with the existing baghouse dust collection system. According to Ingredient Masters CEO Scott Culshaw, this timeline is fast, but not unusual. “The modularity of these systems and the use of our standard dispensers makes a six- to seven-week turnaround possible,” he says. “It also contributes to a very attractive cost. The custom powder batching systems we’re engineering today are being manufactured here in the U.S. at a price point companies expect for used equipment. When you combine the return on investment advantage with the operational benefits, it makes a compelling case.”
Operational Benefits
For Tyrolit, operational benefits have been realized in several important ways. According to Hegener, “More material is being processed, product waste has been reduced and quality has been enhanced.”
In addition, “delays from change-outs have been eliminated, and the maintenance needed to keep the area clean has been reduced,” he says. The system is also well accepted by workers. “We estimate that improvements in all of these areas is at least 10%-and greater in some areas,” adds Hegener.
Tyrolit has subsequently implemented an Ingredient Masters system to upgrade its bond blending operation, which produces bonds for future use. Another batching system is planned for Tyrolit’s facility in Mexico.
As seen in Ceramic Industry magazine, November 2005.