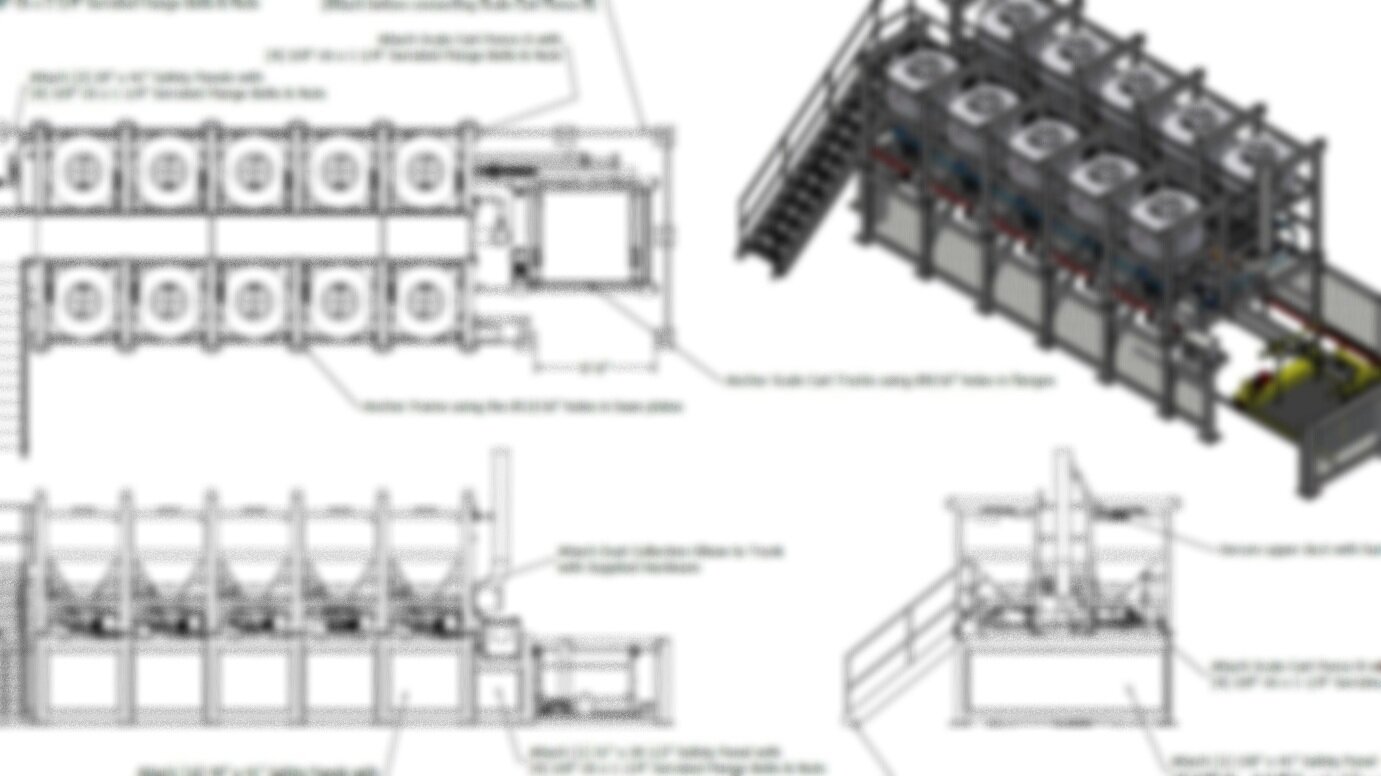
Case Study:
Calhoun Bend Mill
A Better Way To Store and Handle Ingredients
A bulk ingredient dispensing system helps a quick-mix food producer eliminate waste, reduce costs, and increase plant productivity.
Calhoun Bend Mill, located in Jonesville, La., produces a variety of quick food mixes for Southern-style desserts, breads, and fried foods. The family-owned business began in 1987, when brothers Jesse and Patrick started making ground cornmeal in a small room measuring 20 feet by 20 feet. Today, the company employs 20 operators at a new, larger facility.
The Calhoun family settled in the Jonesville area nearly a dozen generations ago. Co-owner Jesse Calhoun, who serves as vice president and plant manager for Calhoun Bend Mill, is among the long family line to have lived in the area. “The surrounding communities called that spot where the Black River makes a large bend Calhoun Bend because of the family,” he said. “So that’s how we got our company name.
Hoping to start small and capture a comer of the quick food-mix market, the Calhoun brothers set out to produce a cornmeal much like what they ate as kids. Stone-ground cornmeal has always been a fixture in Southern cooking, Calhoun said. Early grist mills used stones to grind whole com kernels, thus the term stone-ground cornmeal. Calhoun said the process retained most of the corn’s nutrients by using the entire kernel – a process the brothers wanted to preserve when they established their operations.
“It’s a slow grinding process,” Calhoun said. “But it produces a better product. [The product] has all the vitamins and minerals from the corn. We don’t take anything out. We don’t take out the starch or the oil from the corn kernel prior to grinding like other cornmeal producers do.”
As Calhoun Bend Mill grew, the company began to expand its product line to include mixes for corn bread and hush puppies. In 1989, Calhoun Bend Mill began producing a quick peach cobbler mix, which rapidly became popular and helped expand the company’s reach from regional to national markets.
“We make about 20 different items that are all Southern types of foods – meaning foods that we would eat maybe two or three times a week as part of our diet in the South,” Calhoun said. “What we’ve found is that people all over the United States like them too.”
Calhoun Bend Mill quick mixes are now sold in all 50 states and online at the company’s Web site. Among the products the company now produces are mixes for corn breads, chicken fry coating, onion blossom coating, cobblers, and pies.
“We didn’t invent peach cobbler or stone-ground cornmeal or corn bread mix,” Calhoun said. “But I would say we were probably one of the first ones out there who was doing a stone- ground corn bread mix where all the consumer has to add is eggs and milk. At the time we started, we had products that had a unique preparation and our packaging was fairly different. We got into a lot of markets that normally take a long time and a lot of extra money to get into.”
The many quick mixes are made from flour, sugar, brown sugar, salt, baking powder, baking soda, cornstarch, pepper, and white pepper. The major ingredient in each product is wheat flour or cornmeal flour. The flours have a bulk density of 40 lb/ft³.
With a single ribbon blender and processing line, the mill produces one product at a time. In the past, all of the major quick-mix ingredients arrived in 50-pound bags, stacked on pallets. An operator cut open each bag as required by the recipe and emptied it into the ribbon blender. “The blender mixes around 2,500 pounds, so most of our time was spent filling the blender,” Calhoun said. “We spent as much as an hour or two just filling the blender and opening these bags [to fill the blender once].” An each recipe blends for only about 10 minutes.
From the blender, the product was discharged into a stainless steel container. The containers were taken to packaging, which consisted of three baggers: two form-fill-seal baggers and a valve bagger which fills some of the smaller bags. The form-fill-seal baggers produced a bag as small as the 6-ounce bag for hush puppy mix or as large as a 5-pound bag of mix for chicken fry coating, fish fry coating, or onion blossom coating for food service use. Calhoun Bend Mill also uses its baggers to custom-package products for businesses across the country.
Paper bags generate waste, slow process
When filling the ribbon blender with the proper ingredients for a batch, operators had to empty each 50-pound ingredient bag by hand. This was heavy, repetitive work for the operators, putting them at risk for injury. The process was also inefficient. Handling several hundred pounds of ingredients in 50-pound units made the process slow, Calhoun said, which kept labor costs high. Emptying the ingredients into the blender also generated much waste. Product easily spilled from torn bags and coated surrounding areas as operators poured the ingredients.
“We would have a lot of product on the floor just from where it had spilled out of the bags,” Calhoun said. “You try to be careful, but when you’re opening as many as 400 and 500 fifty-pound bags a day, it’s hard to keep totally clean or dust free. It’s almost impossible.”
Calhoun said the empty bags became an additional waste problem that required much cleanup. “Once we opened all these bags, we had to pick them up and take them outside to the dumpster and deal with them,” he said. “We were filling our trash dumpsters every day. [Garbage collectors] would have to come and dump those once a day for us.”
Emptying the blender was a chore. Once the ingredients were mixed, the finished product was discharged into stainless steel containers to be taken to packaging. The large blender would fill two containers and part of a third before it was emptied. Each container had to be taken to packaging and suspended above the baggers before it could be emptied and then filled again. “So we were spending a lot of time loading and unloading this blender,” Calhoun said.
He said the system inhibited the plant from meeting customer demand.
Calhoun Bend Mill could package between 10,000 and 12,000 pounds of quick mixes each day. But this wasn’t enough. In the peak season, 3 months prior to the Christmas holidays, a second shift was required to meet demand.
In search of something…anything
The Calhoun brothers’ company had grown, and they knew they couldn’t continue to expand the business by producing quick mixes the way they always had. The prime target for change: the 50- pound bags of major ingredients. The Calhouns wanted to reduce spillage and the cleanup associated with dust and empty bags. They also wanted to reduce the risk of worker injury, all while increasing production. Without really knowing what they were looking for, Patrick and Jesse Calhoun went to the Powder & Bulk Solids Exhibition in Chicago in 1994.
“It was kind of a fact-finding show for us, just to see what was out there,” Calhoun said. “We didn’t really know what we needed, but it was an educating show for us. When we make purchases, we try to make them when we’ve had almost a year to think about them, to prepare and then make sure we’ve made the best choice.”
Following the trade show, the brothers looked through many brochures about bulk solids handling systems. They also looked at a few similar food manufacturer’s operations, but most plants they visited weren’t much more efficient than their own.
Many salespeople made their pitches as well. “We had some people try to sell us on bulk handling systems that had flour silos and some really high-dollar equipment that was not justifiable for us at the time,” Calhoun said. “We just could not justify spending half a million dollars on a bulk handling system.”
Most of the systems the Calhouns considered operated very differently from one another. Some were pneumatic. Others harnessed gravity to move materials. But most of the systems could not be upgraded or expanded. “Either you get the whole package to make the system work, or you get nothing,” he said.
Expandability was an important criterion in the Calhouns’ search for a bulk solids handling system. “When you buy a piece of equipment and outgrow it” Calhoun said, “you are going to either put it up to collect dust or, nine times out of ten, you’re going to have to sell it at a loss to someone who absolutely needs it.”
During their search, Jesse and Patrick met a sales representative who knew of a product that might be just what the mill needed. The system the salesperson presented stored ingredients in various-sized polyethylene bins mounted on dispensing stations. Material could be batched into a master dump bin through a hand-operated valve at the bin bottom. Calhoun said the batching system was simple to use and easy to upgrade. And for the small, family-run mill, it seemed “very cost effective,” Calhoun said.
“[The manufacturer] kind of filled in the gap for smaller companies that need to go the next step beyond the 50-pound bags [of ingredients],” he said. “With this system, you can buy the bins and you can empty them manually now. And then down the road you can get a fully automated system and still use the same bins.”
A quick-mix fix
In August 1998, Calhoun Bend Mill installed a Mini-Bulk batching system made by Ingredient Masters. The system’s components include 20 dispensing stations that support frames for 20 various-sized polyethylene dispenser bins.
Calhoun said most of the installation was done by the mill’s staff and a local metal fabricator, but a manufacturer’s representative was always available when help was needed. The installation went smoothly, with only minimal adjustments needed.
Each polyethylene dispenser bin is translucent, which allows ingredient levels to be seen at a glance, and features a top lid for filling. The bins vary from 8 cubic feet, used for minor ingredients, to 100 cubic feet for major ingredients. Each smaller bin’s upper section is square-sided. The larger bins are round at the top. Each bin’s lower section has trapezoidal sides that converge toward the metering valve. The metering valve unloads ingredients to a large dump bin. This dump bin rides on a portable scale cart, which can be positioned under the appropriate bin to weigh the amount of material being loaded.
“The larger bins will hold anything from flour to baking powder to corn starch,” Calhoun said. “Of course, your major ingredients are going to be in your larger bins. If we have an ingredient that we use more often and we’re emptying the bin too often, we can go to a bigger bin. We then can dedicate the smaller bin to an ingredient that isn’t a fast mover. We will always have a use for the equipment.”
Rather than receive the major ingredients in 50-pound paper bags, the plant now receives them in bulk bags. To fill a bin, an operator uses a forklift to move the empty bin from the frame to the floor. The forklift operator then positions a bulk bag filled with an ingredient above the bin, while another operator unties the bulk bag’s outer liner and cuts the inner liner and heat seal, allowing material to flow into the bin. Once an operator screws the bin lid on, the filled bin can be put back in place. For those minor ingredients that still arrive in bags or other containers, an operator fills the bins from a platform at the height of the bin’s lid.
In operation, an operator positions the dump bin, which rides on the scale cart, beneath the appropriate bin and manually opens the metering valve, cutting off the flow of material when the desired amount has been dispensed. For smaller portions a portable scale and small polyethylene container are used to collect the material from the bin. Each of the ingredients is placed into the dump bin, which is then placed on a frame above the blender and discharged of its unmixed contents. Not only did the batching system allow ingredients to be received in bulk bags, it also changed the way the mixed final product was delivered to the bagger.
“[The manufacturer] showed us how we could retrieve the blended batch [in a bulk bag] and go directly to our packaging machines,” Calhoun said.
Now when a batch is mixed and ready for packaging, the blender’s contents are discharged into a large bulk bag which holds roughly 2,500 pounds of product.
“We can empty the entire blender into this bulk bag,” Calhoun said. Each bulk bag of finished product is then mounted on a dispensing frame, also provided by the equipment manufacturer, to unload product to the baggers.
Bulk dispensers save time, cleanup, and money Since installing the bulk dispensers at the plant, Calhoun Bend Mill has been able to save money in many ways. The company can now purchase ingredients in bulk bags, which reduces the cost. But the most significant impact the system has made on the mill’s process is time. “Eliminating the handling of the fifty-pound bags and having our ingredients available in the bins saves time,” Calhoun said. “Whenever you fill the blender, it’s one dump. And when you empty it, it’s one dump. You don’t have to change out a container, fill it, and put another container under the blender and fill it. [The manufacturer] designed the system so we could have a one-dump fill [of the blender] and a one-dump empty.”
The bulk dispensers have also allowed the plant to manage its production time better. In the past when the ingredients were mixed and put into smaller stainless steel containers, the mixture was immediately sent to packaging. Calhoun said the stainless steel containers were expensive and took up too much space to have many of them on hand. Since the blended material is now stored in bulk bags before it’s packaged, operators can fill many bulk bags of material ready for packaging. “So now the operator who works here during the day in the blending room can blend up enough product for the day crew and the night crew if necessary. Now, he’s able to do the job of two shifts in one shift,” Calhoun said. “The [stainless steel containers] were probably ten times as expensive as bulk bags. And once the bag is empty, you can roll it up and put it away [for reuse]. You don’t have a lot of space that’s taken up.
“In the past, the baggers would be waiting for product from the blender. Now, the blender is ahead of the baggers.”
The bulk dispensers have also saved Calhoun Bend Mill money by reducing the amount of waste and dust produced. By opening fewer bags and by using the metering valves to dispense the ingredients from the bins, operators have eliminated most of the dust in the plant. The plant has greatly reduced trash output. By creating a much smoother process, Calhoun said, the bulk dispensers have made the plant more efficient.
“I’d say we probably reduced our labor cost by 25 percent, in both production and cleanup,” Calhoun said. “And I’d say we increased production by as much as 50 percent on some items with the [bulk dispenser] setup.”
Using the old methods, the plant packaged up to 12,000 pounds of quick mix each day. The plant now packages between 18,000 and 20,000 pounds daily. Calhoun said that when the plant concentrates on a single product that is packaged in the larger 5-pound bags, the plant has been able to package as much as 25,000 pounds in a single day.
“We have a more consistent product, a lower ingredient cost, and reduced risk of injuries. I would say it’s a safer setup,” Calhoun said. “Trash dumpsters are only picked up once a week, and cleanup time has been reduced. We have a simple fail-safe system. You almost have to be brainless to not be able to operate this.”
As seen in Powder and Bulk Engineering January 2000.