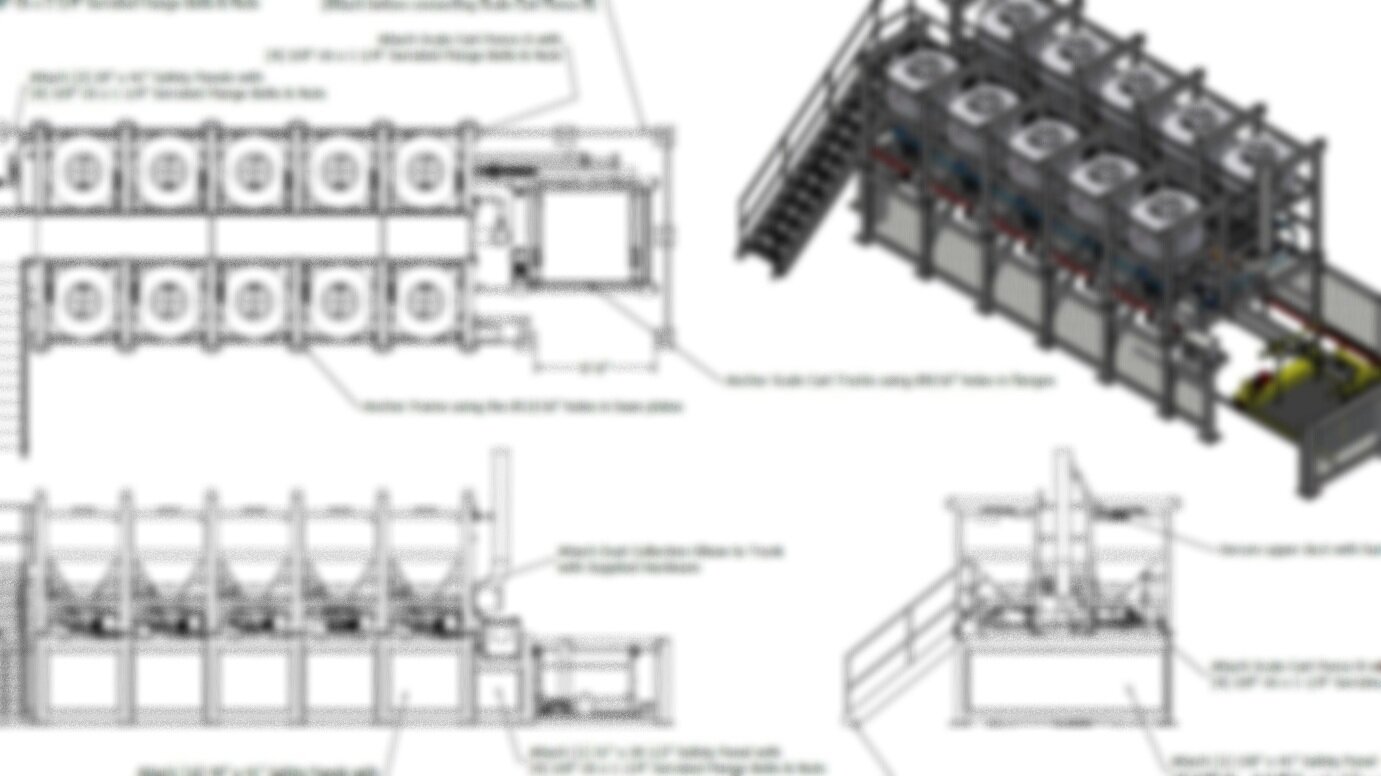
Case Study:
Bear Metallurgical
Bear’s Perfect Ingredient: How Bear Metallurgical managed high-weight materials and tight-tolerance specifications
Bear Metallurgical Company is a leading provider of high-purity ferroalloys and toll-oxide processing for the specialty steel, automotive and foundry industries. It is the sole independent converter of ferrovanadium and ferromolybdenum in the U.S. Processing services provided by the company include the toll conversion of vanadium oxide to ferrovanadium and the conversion of molybdenum oxide into ferromolybdenum.
According to operations manager Bill Snyder, Bear Metallurgical has been successful, in part, because it fully-embraced ‘lean-event’ thinking, and lean-manufacturing strategies, before they became critical to staying competitive, and because management leveraged its commitment to ‘green’ operations by eliminating wasted effort, and wasted material, at every opportunity.
With economic forecasts beginning to darken, mid-2008 might have seemed to be an odd time for capital investment. Bear Metallurgical, however, regarded it as an opportunity to ramp-up efficiency, eliminate some handling costs and prepare for the next growth cycle.
The capital equipment they had in mind was a dry ingredient batching system that would deliver very high (+1 pound on a recipe of 8,500 to 10,000 pounds) accuracy and could accelerate the production cycle for each batch.
Also on the company’s wish list: The elimination of non-productive material handling, specifically, two forklifts and other dedicated mobile equipment used to dispense material to drums; the improvement of safety, hygiene, and housekeeping through reduced dust emissions; and the elimination of redundant weighing and packaging steps. Finally, they wanted greater productive capacity—without disruptions to production, which runs 12 hours-per-day, 5 days-per-week.
Bear Metallurgical’s team requested outline proposals from several nationally-known manufacturers of dry ingredient batching systems. In a unanimous decision, the team selected a concept proposed by Ingredient Masters, Inc.
“Ingredient Masters was a logical fit for us,” says Dave Carey, plant manager. “They had solid credentials with major companies in the refractories and specialty metals field, and they demonstrated, with site visits, that their system could meet our tolerances.”
The system that Ingredient Masters engineered for Bear Metallurgical is custom to their requirements, although it is based on a robust design that the Cincinnati firm has used with excellent results for other precise batching applications.
Raw materials, including reagents, oxides and other ingredients, are delivered in 4,000-pound bulk bags, which are emptied into one of 12 dedicated dispensers, each of which has integral dust control. Dispensers are also fitted with air pads to prevent bridging (compaction). Computer-controlled vibrators pulse the pads at frequencies tailored to each material.
Because the raw materials are exceptionally heavy, these 110 cubic-foot polyethylene dispensers have 5/8-inch nominal wall thickness and 1-inch bottoms. Each dispenser has a capacity of 30,000 pounds. Dispensers are mounted on a steel frame, and are linked by a track, on which a scale cart runs during the batching process.
At the start of the process, the operator specifies whether single or multiple batches will be run, and selects a recipe. The HMI consists of an Allen Bradley compactLogix control processor and Rockwell Software RSView 32 HMI package. System control resides in the PLC with the HMI package providing supervisory control and data acquisition. The user interface contains a full system overview screen, manual operation screens and alarm monitoring screens.
Recipes reside in Microsoft SQL data tables on the same supervisory PC. Recipes contain information on required ingredients, tolerances per ingredient, and system-specific data such as valve position requirements and vibration sequencing. There is no limit to the number of recipes that can be stored within the HMI.
When a recipe is selected, the system informs the operator if any of the required ingredients is not available in the quantities required. Once the batches are initiated, the scale cart begins operation.
Fifty-eight cubic-foot hoppers fit on the scale cart, and, as they move past dispenser stations, weigh and add ingredients as needed. A typical recipe requires five to six ingredients; customers specify the required quality, yield, percent reagent content, and purity. A typical batch is 8,500 to 10,000 pounds. During dispensing, the system logs the appropriate data, halting progress and alerting the operator if dispensing results in metrics that are outside the tolerances specified. No further operator action is required during automatic operation.
As the cart indexes and the bins dispense, run data is displayed. This includes batch start and end time, recipe ID, and the amount of each ingredient required and dispensed. The finished batch is then blended in a double-cone or V-blender.
The Ingredient Masters system is set-up to accommodate enterprise controls in 2010; for now, controls are autonomous, linked to the server, where a tech service manager writes and modifies recipes.
The batching system has achieved the objectives the Bear team established for it. “It is literally everything we expected,” says Dave Carey, “and accomplishes all we wanted it to. In addition to eliminating handling steps that added no value, we were also able to eliminate three high-maintenance scales that required quarterly calibration. Plus, the system is robust and ‘worker-proof,’ with zero unscheduled downtime.”
As seen in Processing Magazine, October 2009.